AMÉLIORATION DE L'EFFICACITÉ ÉNERGÉTIQUE DES SYSTÈMES DE CHAUFFAGE
Une approche systématique d'amélioration de l'efficacité énergétique des chaudières, plutôt que des améliorations faites sans méthodes, comprend quelques étapes simplifiées telles qu'elles sont présentées dans la figure 2.
Figure 2. Programme d'amélioration de l'efficacité des chaudières
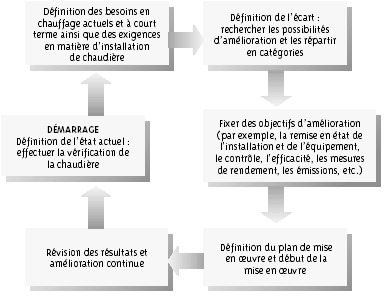
Version - textuelle - figure 2
Figure 2. Programme d’amélioration de l’efficacité des chaudières
Les étapes suivantes feront partie d’un cycle :
- Démarrage – Définition de l’état actuel : effectuer la vérification de la chaudière
- Définition des besoins en chauffage actuels et à court terme ainsi que les exigences en matière d’installation de chaudière
- Définition de l’écart : rechercher les possibilités d’amélioration et les répartir en catégories
- Fixer des objectifs d’amélioration (par exemple, la remise en état de l’installation et de l’équipement, le contrôle, l’efficacité, les mesures de rendement, les émissions, etc.)
- Définition du plan de mise en œuvre et début de la mise en œuvre
- Révision des résultats et amélioration continue
Une vérification de la chaudière (voir la liste de contrôle simplifiée pour la vérification à l'annexe) permettra probablement de déceler les pertes et les inefficacités énergétiques. L'objectif d'une gestion de l'énergie adéquate est de minimiser ces anomalies et les résultats peuvent être importants tant en ce qui concerne les économies que les émissions.
La figure 3 donne un aperçu pratique des éléments qui doivent être visés par les activités de conservation de l'énergie. Toutefois, quelle que soit l'importance de l'exploitation économique et efficace d'une chaudière, il ne faut pas se contenter d'examiner ce seul point. Si l'objectif est de réaliser des économies et d'améliorer la récupération d'énergie, il est néces-saire de vérifier les éléments suivants :
- Les besoins en chauffage et les aspects de l'effica-cité énergétique des procédés, des produits et des pièces d'équipement consommant de la chaleur;
- Les systèmes de distribution de chaleur (tels que la vapeur et le condensat).
La réduction des pertes de chaleur et d'énergie d'une chaudière peut être réalisée grâce à plusieurs méthodes dont certaines comme la production combinée de chaleur et d'électricité (cogénération) sont élaborées et complexes. D'autres, au contraire, sont faciles à appliquer et offrent de bons résultats.
Figure 3. Équilibre énergétique type d'une chaudière ou d'un système de chauffage (avant les améliorations)
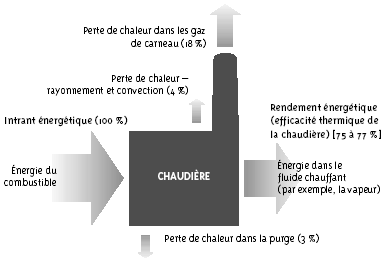
Version - textuelle - figure 3
Figure 3. Équilibre énergétique type d'une chaudière ou d'un système de chauffage (avant les améliorations)
Énergie du combustible rentre la chaudière (intrant énergétique 100 p. 100). De la chaudière, 4 p. 100 de la perte de chaleur est de le rayonnement et convection, 18 % est dans les gaz de carneau et 3 p. 100 est dans la purge. Énergie dans le fluide chauffant (par exemple, la vapeur) sort de la chaudière. Le rendement énergétique (efficacité thermique de la chaudière) est de 75 à 77 p. 100.
Exemples récents : Une usine de produits chimiques réalise des économies de 500 000 $ par an car on y a vérifié et remplacé tous les purgeurs de vapeur qui fuient. Une usine de contreplaqué a réduit sa charge de vapeur de 2 700 kg/h (6 000 lb/h) car on y a amélioré l'isolation de la tuyauterie.
En abaissant la pression de la vapeur ou la température de l'eau du système en fonction des besoins réels des procédés utilisés, il est également possible de réduire la consommation d'énergie.
Les objectifs d'amélioration de l'efficacité énergétique se répartissent dans les principales catégories suivantes.
FONCTIONNEMENT ADÉQUAT DE LA CHAUDIÈRE
Garder la chaudière propre
À l'exception du gaz naturel, presque tout combustible laisse une certaine quantité de dépôt sur les parois des tuyaux exposées aux flammes. Ce dépôt, appelé encrassement, réduit fortement le transfert de chaleur. Des tests ont démontré qu'une couche de suie de 0,8 mm (0,03 po) seulement entraîne une réduction du transfert de chaleur de 9,5 p. 100 et qu'une couche de 4,5 mm (0,18 po) provoque une réduction de 69 p. 100. En conséquence, la température des gaz de carneau augmente, tout comme le coût de l'énergie.
Les chaudières consommant des combustibles solides (tels le charbon et la biomasse) ont une forte tendance à l'encrassement, alors que celles alimentées aux combustibles liquides (particulièrement les huiles filtrées) ont moins tendance à s'encrasser. Pour maintenir l'efficacité optimale de la chaudière, il faut que les surfaces de cette chaudière restent aussi propres que possible. Les chaudières de grande dimension et celles alimentées avec des combustibles qui ont une forte tendance à provoquer un encrassement, sont munies de systèmes de soufflerie permettant d'éliminer la suie sur les parois exposées aux flammes pendant le fonctionnement. On peut également utiliser des brosses et des lances d'arrosage manuelles. Il est recommandé d'ouvrir régulièrement les petites chaudières, notamment celles alimentées au gaz naturel et celles n'incluant pas de souffleurs de suie, afin de les vérifier et de les nettoyer.
Les dépôts (appelés tartre) qui se retrouvent sur les parois mouillées des tubes de la chaudière peuvent entraver le transfert de chaleur, réduire l'efficacité de la chaudière, restreindre la circulation de l'eau et entraîner de graves problèmes mécaniques et de fonctionnement. Le tartre provoque une hausse de la température du métal des tuyaux, entraînant ainsi une augmentation de la température des gaz de carneau. Dans les cas extrêmes, les tubes deviennent défectueux en raison de la surchauffe.
Il faut se rappeler qu'une accumulation d'un millimètre de tartre peut entraîner une augmentation de 2 p. 100 de la consommation de combustible.
Au lieu de fermer et de purger les chaudières pour effectuer une vérification visuelle de la propreté des parois mouillées, on peut vérifier l'eau de la chaudière en effectuant des tests pendant qu'elle fonctionne; selon les résultats, on peut injecter certains produits chimiques de traitement de l'eau. Dans les petites installations à basse pression, l'eau de la chaudière est vérifiée quotidiennement et dans les grandes installations à haute pression, toutes les heures. Le programme d'essai et de traitement de l'eau est important pour assurer l'efficacité maximale et le fonctionnement fiable de toute installation de chaudière.
Une tendance continue à la hausse des températures des gaz de carneau pendant des semaines ou des mois indique en général qu'un dépôt s'est accumulé, soit sur les parois exposées aux flammes, soit sur les parois mouillées d'échange de chaleur de la chaudière. Dans ce cas, il faut vérifier la chaudière dans les moindres délais.
Éviter l'entrée d'air indésirable
Le contrôle efficace de l'air comburant en excès (tel qu'il a été abordé antérieurement) comprend également la protection contre l'infiltration d'air indésirable dans la cavité de combustion de la chaudière ou le système de carneau. L'air entre par les couvercles qui fuient, les lunettes d'observation, les joints défectueux et les autres ouvertures.
Eau de purge ou gaspillage d'argent
Même traitée (« déminéralisée »), l'eau d'alimentation de la chaudière contient de petites quantités de sels minéraux dissous. L'évaporation continue de l'eau des chaudières à vapeur et de l'eau douce d'appoint provoque l'augmentation de la concentration de ces minéraux et la formation de tartre. Pour éviter ce problème, l'eau de la chaudière doit être régulièrement purgée. En général et par précaution, cette opération est effectuée avec excès. L'eau de purge est chauffée, ce qui entraîne donc un gaspillage d'énergie, d'eau et de produits chimiques de traitement. Une mesure de prévention minimale consiste à vérifier régulièrement l'eau de la chaudière pour déterminer le niveau de matières solides dissoutes et régler le taux de purge.
Si la purge est effectuée une fois par jour ou à tous les quarts de travail, la concentration en matières solides dissoutes immédiatement après la purge est très inférieure au maximum acceptable. Si la purge peut être effectuée plus souvent en utilisant une plus petite quantité d'eau, ou continuellement, la concentration en matières totales dissoutes (MTD) peut être maintenue plus près du niveau maximum de sécurité recherché. Le contrôle de la concentration en MTD est l'élément le plus important. On trouve sur le marché des dispositifs de contrôle automatique de purge permettant la mesure continue de la concentration en MTD.
Exemple : Envisager une chaudière de 23 t/h fonctionnant à 860 kPa (environ 50 000 lb/h à 125 lb/po2). L'eau de purge contient 770 kJ/kg (330 Btu/lb). Si le dispositif de purge en continu est réglé à la valeur habituelle de 5 p. 100 de l'évaluation maximale de la chaudière, le débit de purge serait de 1 150 kg/h contenant 885 500 kJ (environ 2 500 lb/h contenant 825 000 Btu). À une efficacité de 80 p. 100, cette chaleur requiert environ 29,7 m3/h (1 050 pi3/h) de gaz naturel, d'une valeur approximative de 32 100 $ par an (fondé sur 300 jours par an à 0,15 $/m3).
De toute évidence, les systèmes de chaudière à eau chaude ne sont pas à l'origine de coûts de purge.
Maximiser le retour du condensat chaud
Le système à vapeur et à condensat doit être conçu de sorte que l'on puisse éliminer le coup de bélier et réduire les pertes et l'entretien.
Si une chaudière à vapeur subit une perte de condensat, on constate que la consommation d'eau est plus élevée, l'utilisation de produits chimiques de traitement de l'eau est plus fréquente et la production d'énergie thermique nécessaire pour chauffer l'eau d'appoint est accrue. Quand il y a retour du condensat, c'est-à-dire lorsque la pression du procédé est relâchée dans le réservoir de retour du condensat, de l'énergie supplémentaire est perdue sous forme de vapeur de détente. On peut minimiser de telles pertes, par exemple en immergeant l'entrée de retour du condensat dans le réservoir ou en installant un condenseur de buées à arrosage sur le dessus du réservoir.
Un système à circuit fermé fournissant un condensat de vapeur sous pression à rebouillir permet presque d'éliminer les pertes et requiert moins d'équipement de traitement de la vapeur.
Exemple : Récemment, une société minière du Québec a installé un système à condensat à circuit fermé. Elle a rapidement réduit de 18 p. 100 sa consommation d'énergie dans la chaufferie comparativement à un système à condensat de vapeur conventionnel à circuit ouvert.
RÉCUPÉRATION DES PERTES DE CHALEUR DE LA CHAUDIÈRE
Gaz de carneau
Il s'agit de la meilleure occasion de récupération de chaleur dans la chaufferie.
Une réduction de 20 ºC (36 ºF) de la température des gaz de carneau permet d'améliorer l'efficacité de la chaudière d'environ 1 p. 100.
Même avec des brûleurs bien réglés fournissant des températures minimales de gaz de carneau, tout en réalisant une consommation complète du combustible, les températures de sortie de ces gaz peuvent normalement varier de 175 ºC (350 ºF) à 260 ºC (500 ºF). Il est encore possible de récupérer une partie de cette chaleur qui sinon « s'échapperait par la cheminée ». Les échangeurs de chaleur peuvent être utilisés pour préchauffer l'eau d'alimentation de la chaudière (économiseurs) ou l'air comburant (réchauffeurs). En général, les économiseurs permettent une amélioration de 3 à 4 p. 100 de l'efficacité globale de la chaudière.
Les concepteurs et les opérateurs d'économiseurs doivent prendre en considération les problèmes de corrosion éventuels, en particulier dans les combustibles contenant du soufre. L'humidité contenant de l'acide sulfurique corrosif risque de se condenser sur toutes les surfaces des échangeurs de chaleur dont la température descend sous le point de rosée acide. En général, ce phénomène se produit près de l'entrée d'air comburant ou d'eau d'alimentation à chauffer.
Chaque chaudière a une limite particulière de basse température de gaz de carneau qu'il faut déterminer individuellement si l'on envisage un échange de chaleur complémentaire. Comme les températures des gaz de carneau sont plus basses à des charges faibles, les économiseurs sont souvent équipés d'un dispositif de contrôle de dérivation permettant de maintenir ces températures au-dessus d'un minimum préétabli.
Les économiseurs à condensation permettent d'améliorer l'efficacité de la récupération de la chaleur des gaz de carneau en refroidissant ces gaz à une température sous le point de rosée acide. Ils permettent ainsi de récupérer tant la chaleur sensible provenant des gaz de carneau que la chaleur latente de l'humidité qui condense. Il peut y avoir de l'humidité dans le combustible, mais la plus grande partie se forme par combustion de l'élément d'hydrogène du combustible (voir « Perte causée par l'humidité engendrée par la combustion de l'hydrogène », page 2). Comme la condensation (et le risque de corrosion qui en découle) est inévitable, le système d'échange de chaleur doit être fabriqué avec des matériaux qui ne se corrodent pas. Dans les économiseurs à contact direct, l'eau est vaporisée directement dans les gaz de carneau et l'eau chaude qui est ainsi générée est recueillie et utilisée après traitement afin de neutraliser son potentiel de corrosion. (Il s'agit d'un avantage secondaire de la condensation des gaz de carneau à contact direct : elle élimine les particules et les gaz acides tels le SO2 provenant de l'évacuation.) Grâce aux économiseurs à condensation, les rendements globaux des chaudières peuvent être supérieurs à 90 p. 100. Les thermopompes peuvent compléter un système de récupération de la chaleur des gaz de carneau, améliorant ainsi davantage l'efficacité de la récupération.
Exemple : On a installé des économiseurs à condensation à contact direct à l'Hôpital du Sacré-Coeur de Montréal. La chaleur récupérée a servi pour le chauffage à eau chaude des locaux, la climatisation, le blanchissage, l'alimentation en eau chaude sanitaire et la cuisine. Ces mesures ont permis de réduire de 11 p. 100 la consommation de gaz naturel et de diminuer les émissions de CO2 de 12 000 t.
Récupération de chaleur générée par la purge
Nous avons présenté auparavant quelques moyens permettant de limiter le volume de purge et la perte de chaleur. Les échangeurs thermiques peuvent récupérer la chaleur sensible générée par la purge et s'écoulant dans le réseau d'égouts afin de chauffer l'eau d'appoint de la chaudière et effectuer d'autres activités similaires.
UTILISATION ET DIMENSIONNEMENT DE LA CHAUDIÈRE
Si une chaudière doit être remplacée ou si elle requiert des améliorations importantes, il faut revoir son utilisation et ses dimensions. De nombreuses installations de chaudière, en particulier celles utilisées pour le chauffage des locaux, doivent répondre à des besoins qui varient considérablement en raison des saisons ou d'autres éléments. Lorsque la chaudière a un rendement de 40 p. 100 inférieur à la capacité maximale évaluée, son efficacité à convertir l'énergie du combustible en vapeur ou en eau chaude chute fortement à charge faible. Par conséquent, il est logique de choisir des chaudières en fonction de leurs dimensions et des divers besoins. Une petite chaudière pourrait être installée pour fonctionner presque à pleine charge pendant les périodes où la demande est faible et une ou deux chaudières de plus grande capacité pourraient subvenir aux besoins de charges de pointe.
Dans l'évaluation de l'utilisation et des dimensions d'une chaudière, il faut prendre en considération les exigences actuelles et futures de chauffage et de vapeur industrielle. Au cours de la révision du procédé et de l'équipement connexe, de nouvelles possibilités d'améliorations éconergétiques peuvent se présenter.
Exemple : Au pénitencier de la Saskatchewan, on a installé deux nouvelles chaudières de petite dimension, adaptées aux charges correspondant à l'été (fonctionnement individuel) et pouvant fonctionner en parallèle pendant l'hiver. On a remplacé les anciennes chaudières surdimensionnées qui fonctionnaient à débit réduit pendant la plus grande partie de l'année. Cette solution a entraîné une amélioration de l'efficacité à des taux de combustion plus élevés. En ce qui concerne les locaux chauffés, les économies de gaz correspondaient à 500 000 m3 (17 p. 100) et s'élevaient à 75 000 $ par an, et les émissions de CO2 ont chuté en conséquence. Les nouveaux brûleurs à faible émission de NOx ont permis de réduire les émissions d' oxyde d' a zote de 70 p. 100.
PRODUCTION COMBINÉE D'ÉLECTRICITÉ ET DE CHALEUR – COGÉNÉRATION
Les anciennes chaudières inefficaces requièrent souvent des remises en état importantes et coûteuses. Dans ce cas, s'il y a des demandes de chauffage et d'électricité ou si l'électricité peut être vendue à profit, on peut envisager la cogénération ou la production combinée d'électricité et de chaleur. Au Canada, le plus grand potentiel des systèmes de cogénération consiste à remplacer, dans l'ensemble du pays, des milliers de petites chaudières trop anciennes par des installations produisant de l'électricité et de la chaleur. Cette solution permet une meilleure efficacité que si l'électricité et la chaleur étaient générées séparément.
La cogénération peut requérir plus de combustible et une quantité beaucoup plus importante de capital que ce qui est nécessaire pour simplement répondre aux besoins en chaleur. Toutefois, l'énergie électrique et le rendement thermique supérieur découlant de la cogénération représentent un avantage car l'énergie totale, tant électrique que thermique, est fournie à un coût plus faible. En raison du rendement élevé de l'énergie globale de la cogénération (jusqu'à 85 p. 100), des avantages pour l'environnement se traduisant par une réduction des émissions de CO2 et de NOx, ainsi que de la déréglementation actuelle du marché canadien de l'énergie, on s'intéresse de plus en plus à cette technologie qui évolue rapidement.
Une installation de cogénération type se compose d'un moteur d'entraînement tels une turbine à gaz ou un moteur à piston et d'un générateur de vapeur à récupération thermique qui est un genre de chaudière. Le moteur commande un générateur électrique et parfois d'autres appareils, tels que des compresseurs d'air. L'évacuation, par le biais du générateur de vapeur, fournit de la chaleur pour le chauffage ou l'utilisation industrielle. À présent, on trouve des installations de cogénération dont le rendement varie de quelques kilowatts à des dizaines de mégawatts.
Pour évaluer un produit de cogénération éventuel, il est nécessaire de consulter un spécialiste.
AUTRES CONSIDÉRATIONS
Pour optimiser le rendement et améliorer l'efficacité énergétique d'une chaudière, il faut considérer certains facteurs, tels l'entretien régulier et les petites remises en état. Quand il s'agit d'apporter une amélioration importante, il faut également tenir compte d'autres facteurs.
Isolation
La vérification d'une chaudière peut permettre de déceler une isolation et une tuyauterie inadéquates requérant une réparation ou un remplacement complet.
Exemple : Si seulement dix brides d'une canalisation de 10 cm (4 po) de diamètre supportant de la vapeur à 860 kPa (125 psi) ne sont pas isolées, la perte de chaleur annuelle équivaut à 2 450 m3 de gaz naturel (valant 370 $).
Exemple : Une canalisation de vapeur de 3 m (10 pi) de long non isolée entraîne un gaspillage en coûts de production de vapeur correspondant à plus du double du prix de son isolation au moyen de fibre minérale et de gaine en aluminium.
Besoins en chauffage
La réduction de la pression de fonctionnement de la vapeur de la chaudière au minimum requis par l'utilisateur final ou la diminution de la température du fluide circulant dans les tuyaux des systèmes de chauffage peut avoir des répercussions importantes sur les économies d'énergie et la quantité de gaz à effet de serre générés. Ces économies sont le résultat d'une diminution de la consommation de combustible du système de chauffage et de la quantité de perte de chaleur du réseau de canalisation.
Pour modifier la pression de fonctionnement de la chaudière ou la température du fluide, s'assurer que la chaudière et les appareils d'utilisation finale peuvent fonctionner à la pression la plus faible (température). Les économies que l'on peut réaliser en termes d'environnement et de coût valent que l'on s'y intéresse.
Pertes d'énergie du système de distribution
Dans les systèmes à vapeur, les purgeurs de vapeur peuvent tomber en panne en moyenne jusqu'à 25 p. 100 du temps. Les fuites de vapeur des raccords de tuyaux, des robinets et des purgeurs peuvent provoquer des pertes d'énergie importantes. De plus, l'eau qui fuit doit être remplacée, traitée chimiquement et chauffée. Il s'agit là de conséquences moins évidentes, mais pourtant coûteuses. Les systèmes au fluide chauffant peuvent également être sujets à ce problème.
Exemple : Dans un système à vapeur de 690 kPa (100 psi), un seul purgeur défectueux de 3,2 mm (1/8 po) peut entraîner une perte de gaz naturel correspondant à 11 600 m3/an et équivalant à 1 700 $.
S'assurer que la dimension de la tuyauterie est adéquate car des tuyaux surdimensionnés peuvent entraîner une augmentation des coûts du capital, de l'entretien et de l'isolation, ainsi que des pertes de chaleur en surface. Par contre, les tuyaux de dimensions insuffisantes exigent une pression plus élevée et une énergie de pompage supplémentaire. De plus, ils présentent des taux de fuite plus importants.
Une tuyauterie désuète et en surnombre entraîne un gaspillage d'énergie. Comme la tuyauterie est maintenue à la même température que le reste du système, la perte de chaleur par unité de longueur de tuyau reste la même. Les pertes thermiques engendrées par la tuyauterie en surnombre augmentent la charge calorifique des locaux et par conséquent, les besoins en ventilation et en climatisation. En outre, la tuyauterie en surnombre est peu entretenue et contrôlée, ce qui engendre des pertes supplémentaires.
Désaération inadéquate de l'eau d'alimentation de la chaudière
Une quantité aussi faible que 1 p. 100 par volume d'air dans la vapeur peut entraîner une réduction de l'efficacité du transfert de chaleur pouvant atteindre 50 p. 100. Surveiller le processus de désaération et vérifier si le fonctionnement des évents est adéquat.
Chaleur en cascade
L'utilisation de la chaleur en cascade peut représenter une excellente occasion d'améliorer l'efficacité énergétique globale des installations dont les besoins en chauffage sont multiples. La chaleur utilisée à une étape du procédé peut servir à chauffer ultérieurement. Il faut diriger la chaleur de haute qualité produite par le combustible vers le procédé requérant les températures les plus élevées et le rejet thermique doit servir pour les demandes de températures plus basses. La chaleur émise à la fin du processus devrait correspondre aux températures les plus basses possibles du point de vue économique.
Exemple : L'air ou le gaz évacué par un procédé requérant des températures élevées circule dans une chaudière de récupération afin de générer de la vapeur à basse pression ou de l'eau chaude pour le chauffage des locaux et de l'eau à usage industriel. Par exemple, la chaleur résiduelle sert également au refroidissement, par le biais du refroidisseur à absorption. On peut récupérer, entreposer et réutiliser la chaleur de diverses manières.
Détails de la page
- Date de modification :