Table des matières
- Organisation du guide
- Buts de ce guide de référence
- Qu’est-ce que l’air comprimé ?
- Introduction aux systèmes d’air comprimé
- Types de compresseurs d’air et dispositifs de régulation
- Équipements auxiliaires des compresseurs d’air
- Usages normaux et usages abusifs de l’air comprimé
- Ainsi, vous vous apprêtez à évaluer un système d’air comprimé ?
- Mesures d’efficacité énergétique éprouvées
- Entretien de votre système d’air comprimé
- Exemples de cas “avant et après”
- Prochaines étapes
- Glossaire
- Documentation et références web
- Conseils pratiques pour optimiser les systèmes d’air comprimé
Organisation du guide
Ce guide comprend 16 chapitres. Son principal objet est de vous aider à comprendre et à mettre en œuvre un programme d'amélioration du rendement énergétique des systèmes d'air comprimé. Combinant des données théoriques et pratiques, le guide comprend également quelques exemples généraux, un glossaire et des références bibliographiques. Les lecteurs souhaitant optimiser très rapidement un système d'air comprimé trouveront des conseils en ce sens au dernier chapitre.
THÈME | Voir les chapitres |
Introduction au Guide | Buts de ce guide de référence Qu'est-ce que l'air comprimé ? |
Systèmes d'air comprimé et leurs composants | Introduction aux systèmes d'air comprimé Types de compresseurs d'air et dispositifs de régulation Équipements auxiliaires des compresseurs d'air |
Réduction de la consommation d'énergie | Usages normaux et usages abusifs de l'air comprimé |
Évaluations de systèmes d'air comprimé | Ainsi, vous vous apprêtez à évaluer un système d'air comprimé ? |
Optimisation continue | Mesures d'efficacité énergétique éprouvées Entretien de votre système d'air comprimé |
Exemples de cas types | Exemples de cas "avant et après" Prochaines étapes |
Références | Glossaire Documentation et références Web Unités de mesure et facteurs de conversion |
Mise en œuvre d'un plan | Conseils pratiques pour optimiser les systèmes d'air comprimé |
Le guide comporte des parties encadrées qui mettent en valeur des conseils sur les économies d'énergie et le fonctionnement des systèmes d'air comprimé.
Les indications relatives aux économies d'énergie figurent généralement dans des cadres en lignes pointillées.
Les points et conseils pratiques essentiels sont entourés d'un cadre en trait plein.
Buts de ce guide de référence
Ce guide de référence traite des systèmes d'air comprimé types couramment utilisés dans la plupart des petites et moyennes installations de production. Consacré aux problèmes courants de conception et de fonctionnement des systèmes d'air comprimé, ce guide a pour but de vous présenter les principes directeurs régissant votre système d'air comprimé, ainsi que les aspects à prendre en compte lorsque vous commencez ou poursuivez l'optimisation de votre système en vue d'un rendement maximal.
Vous vous demandez sans doute pourquoi vous devriez lire ce guide de référence ou vous y reporter. Eh bien, ce guide pourra s'avérer utile si vous vous trouvez dans l'une ou l'autre des situations suivantes :
- Les factures de votre fournisseur d'électricité ne cessent d'augmenter et votre patron vous presse de réduire les coûts d'énergie dans vos installations.
- Vous devez remplacer un vieux compresseur ou agrandir votre système d'air comprimé.
- Vous savez que vous devez "dépanner" votre système d'air comprimé, mais vous ne savez pas trop par où commencer, quels sont les aspects à considérer, ni même où vous adresser pour obtenir les informations voulues.
- La production est entravée par des durées d'indisponibilité trop longues ou du fait d'une pression insuffisante de votre système d'air comprimé.
- Vous devez apporter une solution judicieuse à un client interne ou externe qui éprouve certaines difficultés avec son système d'air comprimé.
Si vous vous trouvez dans l'une de ces situations, c'est que vous assumez probablement l'une des fonctions suivantes :
- Responsable de la production ou de l'entretien, cherchant à réaliser des économies et à accroître la productivité.
- Représentant d'une entreprise d'électricité ayant pour mandat d'aider ses clients à accroître l'efficacité énergétique de leurs installations.
- Représentant en compresseurs d'air ou chargé du développement économique d'une entreprise de service, devant aider ses clients à trouver une solution à leurs problèmes d'air comprimé.
- Étudiant ou stagiaire qui désire acquérir des connaissances en matière de systèmes d'air comprimé.
Les raisons d'être de l'air comprimé
Bien qu'il ne soit pas gratuit, l'air comprimé est malheureusement considéré souvent comme tel. Vous devez être sensibilisé au fait que la production d'air comprimé est coûteuse et qu'elle consomme une tranche relativement importante de votre budget consacré à l'énergie.
Outre les coûts d'exploitation, il se pose aussi des questions de fiabilité et de rendement du système, sans oublier le problème de la qualité de l'air comprimé. Il est possible de déterminer ces coûts directs et indirects en effectuant des mesures sur votre système et en établissant ses données de référence.
Le coût de l'air comprimé est parfaitement contrôlable et ce guide de référence vous aidera à identifier plusieurs méthodes courantes de réduction des coûts d'énergie, d'entretien et en capital liés à la possession et au fonctionnement de votre système d'air comprimé.
Aspects visés et non visés par ce guide
Le présent guide a été rédigé pour aider à vous sensibiliser aux coûts de l'air comprimé et à vous mettre sur la bonne voie de la réduction de ces coûts. Il présente des recommandations et des conseils sur les meilleures pratiques en matière d'efficacité énergétique.
Ce guide est consacré aux systèmes d'air comprimé types que l'on retrouve habituellement dans la plupart des petites et moyennes unités de production. Il traite des problèmes courants de conception et de fonctionnement des systèmes d'air comprimé.
Le guide a pour but de vous présenter les principes directeurs régissant votre système d'air comprimé, ainsi que les aspects à prendre en compte lorsque vous commencez ou poursuivez l'optimisation de votre système en vue d'un rendement maximal.
Ce guide de référence est de caractère général et n'aborde pas tous les problèmes et solutions caractéristiques des systèmes d'air comprimé. Il ne s'agit pas non plus d'un guide aidant à la conception de systèmes d'air comprimé, nouveaux ou en cours d'augmentation de capacité. Ce guide ne remplace pas - ni ne vise à remplacer - les manuels d'utilisation des équipements ou les procédures d'entretien.
Nous recommandons vivement aux lecteurs de respecter les procédures appropriées en matière de santé, sécurité et verrouillage, et de se conformer aux manuels d'utilisation et d'entretien avant, pendant et après toute modification, travail ou essais afférents à des systèmes d'air comprimé. Le non-respect des procédures de santé et sécurité, et des codes appropriés, pourrait entraîner des blessures graves, pertes de vies, dommages matériels, perturbations dans la production et autres risques divers.
Qu’est-ce que l’air comprimé ?
L'air comprimé est une forme d'énergie emmagasinée qui sert à faire fonctionner des machines, des équipements ou des procédés industriels. L'air comprimé est utilisé dans la plupart des industries de fabrication et dans certaines industries de services, notamment dans les cas où l'utilisation directe de l'électricité pour alimenter des outils ou des appareils se révèle peu pratique, voire dangereuse.
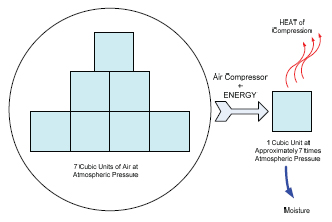
Figure 1 - Conversion de l'air atmosphérique en air comprimé
Version texte
Figure 1 - Conversion de l'air atmosphérique en air comprimé
Diagramme montrant sept unités cubes d'air étant comprimé par un compresseur d'air, ce qui nécessite de l'énergie, et pour produire une unité cube d'air comprimé à aproximately 7 fois la pression atmosphérique, en plus de la chaleur de la compression et de l'humidité.
Un compresseur d'air type entraîné par l'électricité comprime environ 7 volumes d'air à la pression atmosphérique en 1 volume d'air à pression plus élevée (environ 100 psig, ou 7 bars). L'air à haute pression ainsi obtenu est distribué aux appareils ou aux outils dans lesquels il se détend à la pression atmosphérique, libérant ainsi l'énergie nécessaire à leur fonctionnement.
Lors du processus de la compression, et du refroidissement ultérieur de l'air aux températures ambiantes, de la chaleur et de l'humidité se dégagent, comme l'illustre la Figure 1.
On peut utiliser la chaleur récupérée du compresseur d'air comme mesure d'efficacité énergétique se combinant à d'autres procédés : par exemple, le chauffage des locaux et le chauffage de l'eau.
Selon le type d'application, il peut s'avérer nécessaire de contrôler l'humidité en excès dans l'air comprimé à cause des éventuels problèmes éprouvés par les tuyauteries (corrosion) et les équipements utilisés.
Coûts de l'air comprimé
Cette section vous aidera à mieux comprendre ce qu'il en coûte pour la production et l'utilisation de l'air comprimé.
Pendant les dix premières années de vie d'un compresseur classique à refroidissement par air (voir la Figure 2), en marche durant deux quarts de travail, le coût d'exploitation (électricité et entretien) va représenter environ 88 % du coût total de la durée de vie. Le coût initial de l'équipement et de l'installation représentera les autres 12 %.
Du fait que l'énergie représente environ 76 % du coût de fonctionnement global pendant la durée de vie, il est capital de concevoir et d'acheter les composantes les plus efficaces pour votre système d'air comprimé. Il est recommandé de prendre les décisions d'achat en tenant compte des coûts de fonctionnement pour la durée de vie globale prévue et NON pas seulement en fonction du coût initial du matériel.
Figure 2 - Coûts de propriété types du cycle de vie des systèmes d'air comprimé
(source : ministère américain de l'énergie)
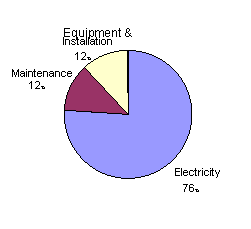
Figure 2 - Coûts de propriété types du cycle de vie des systèmes d'air comprimé
Text version
Figure 2 - Coûts de propriété types du cycle de vie des systèmes d'air comprimé
Diagramme circulaire montrant 76 pour cent du coût de la propriété est de l'électricité, 12 pour cent est pour l'entretien, et 12 pour cent est pour l'équipement et l'installation.
La Figure 3 montre les pertes types liées à la production et à la distribution de l'air comprimé. Par exemple, pour une puissance consommée de 100 HP, environ 91 HP sont perdus alors que seuls 9 HP représentent un travail utile. En d'autres termes, 90 % environ de l'énergie utilisée pour la production et la distribution de l'air comprimé sont habituellement perdues.
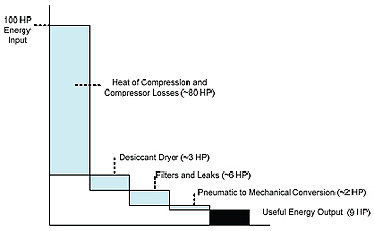
Figure 3 - Énergie consommée pour la production d'air comprimé et énergie utile produite
(avec la permission de Northwest Energy Alliance)
Text version
Figure 3 - Énergie consommée pour la production d'air comprimé et énergie utile produite
Diagramme à barres montrant les pertes typiques associés à la production et la distribution de l'air comprimé départ avec 100 HP apport d'énergie. La première barre montre que Situé à environ 80 HP est perdue sous forme de chaleur de compression et de compression des pertes; la deuxième barre montre que Situé à environ 3 HP sont perdus à la sèche desséchant; la troisième barre montre que Situé à environ 6 HP sont perdus pour les filtres et les fuites, la quatrième bar montre que Situé à environ 2 HP sont perdus à pneumatique à la conversion mécanique; la cinquième barre indique que la production d'énergie utile est de 9 HP.
Demandez-vous toujours si l'air comprimé est bien la source la mieux appropriée pour une application donnée. Dans nombre de cas, il pourrait être préférable d'utiliser un outil entraîné directement par l'électricité plutôt qu'un outil entraîné par l'air comprimé.
Certains compresseurs industriels sont à refroidissement par eau. Dans ces cas, il convient d'évaluer les frais additionnels liés à l'eau et à son évacuation, les coûts de fonctionnement du système de refroidissement de l'eau, et les coûts de pompage et de traitement chimique. La Figure 4 est un tableau simplifié qui donne des indications sur les coûts d'électricité liés à des fonctionnements sur un, deux ou trois quarts de travail dans une installation industrielle classique. Le tableau montre ces coûts pour des compresseurs d'air d'une puissance de 10, 15, 25, 50 et 100 HP. On suppose que la charge moyenne des compresseurs correspond à 65 % de la charge nominale.
À noter que ce tableau emploie un tarif d'électricité mixte (énergie et puissance appelée) de 0,10 $ le kWh. Selon vos tarifs locaux, vous devrez multiplier les chiffres de la Figure 4 par votre tarif d'électricité local (dollars par kWh) et multiplier ensuite le résultat par 10 pour en déduire vos frais annuels d'électricité. En communiquant avec votre entreprise d'électricité locale ou votre fournisseur de services d'air comprimé, ils vous aideront à déterminer votre propre tarif mixte d'électricité.
1 quart (2 250 h) |
2 quarts (4 250 h) |
3 quarts (8 400 h) |
|
---|---|---|---|
10 HP | 1 720 $ | 3 250 $ | 6 430 $ |
15 HP | 2 580 $ | 4 880 $ | 9 640 $ |
25 HP | 4 300 $ | 8 130 $ | 16 060 $ |
50 HP | 8 600 $ | 17 260 $ | 32 130 $ |
100 HP | 17 120 $ | 32 330 $ | 63 900 $ |
Afin de tenir compte des coûts d'entretien et du coût en capital pour la durée de vie (prix d'achat) du système d'air comprimé, ajoutez environ 25 % au coût annuel de l'électricité pour la production de l'air comprimé. Par exemple, un compresseur de 50 HP fonctionnant sur un quart va coûter environ 8 600 $ en électricité seule, plus environ 2 150 $ pour frais d'entretien et coût en capital, soit en tout 10 750 $ annuellement.
Dans la plupart des installations, on peut aisément économiser de 10 à 20 % des coûts d'énergie de production d'air comprimé grâce à un entretien systématique axé sur la réparation des fuites d'air, la diminution de la pression de l'air et le remplacement des filtres colmatés. Des économies plus élevées sont possibles en employant une meilleure régulation des compresseurs, en augmentant la capacité des réservoirs d'air comprimé et en améliorant les sécheurs et filtres d'air.
À partir des informations fournies dans la Figure 4, quelles sont les possibilités de réaliser des économies d'argent et d'énergie dans votre installation ?
Introduction aux systèmes d’air comprimé
Les systèmes d'air comprimé se composent de plusieurs sous-systèmes et composants principaux. Les systèmes d'air comprimé peuvent également être subdivisés en deux parties : le côté production et le côté consommation.
Le côté production comprend les compresseurs, le traitement de l'air et les installations de stockage primaire. Un système bien géré va produire de l'air propre, sec et stable, délivré à la pression voulue de façon fiable et économique. Les principaux sous-systèmes de production d'air comprimé incluent normalement la prise d'air, le compresseur d'air (à vitesse fixe et/ou à vitesse variable), le refroidisseur de sortie, le moteur, les dispositifs de régulation, les équipements de traitement de l'air et les accessoires.
Les dispositifs de régulation servent à régler la quantité d'air comprimé à produire pour maintenir une pression constante dans le système et gérer les interactions entre les divers composants du système. Les filtres à air et les sécheurs d'air éliminent l'humidité, l'huile et les impuretés de l'air comprimé. Le stockage de l'air comprimé (réservoirs humides et réservoirs secs) sert également à améliorer le rendement et la stabilité du système. L'eau accumulée est évacuée par des purgeurs de type manuel ou automatique. Les régulateurs de pression permettent de maintenir une pression constante dans un dispositif final d'utilisation.
Le côté consommation inclut les tuyauteries de distribution, les stockages secondaires et les appareils d'utilisation. Un système de consommation bien géré minimise les différences de pression, diminue les pertes d'air dues aux fuites et aux dispositifs de purge, et procure l'air comprimé aux appareils et applications appropriés. Les tuyauteries de distribution acheminent l'air comprimé, du compresseur aux points d'utilisation finale. On utilise également à des réservoirs d'air comprimé côté consommation afin d'améliorer la stabilité de la pression du système.
Comme règle empirique, pour chaque cheval-vapeur (HP) de puissance nominale, un compresseur d'air va produire environ 4 pieds cubes normaux par minute (pcnm).
Un schéma simplifié montrant comment sont raccordées les principales composantes d'un système d'air comprimé est présenté dans la Figure 5.
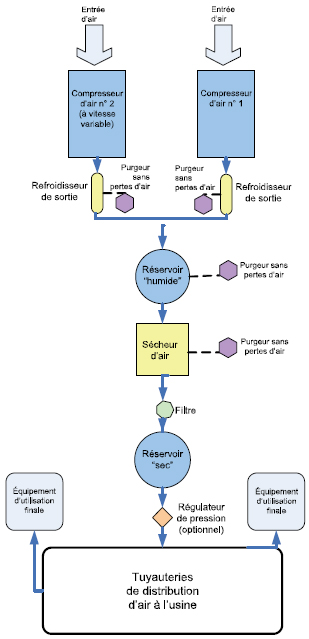
Figure 5 – Composantes d'un système classique d'air comprimé
Version texte
Figure 5 – Composantes d'un système classique d'air comprimé
diagramme montrant les compresseurs d'air, refroidisseurs, récepteur « humide », sécheur d'air, filtre, récepteur « à sec », régulateur de pression, tuyaux de distribution d'air, et l'utilisation finale des équipements.
Emplois de l'air comprimé
L'air comprimé est courant dans de nombreuses applications commerciales et industrielles. Du fait de son emploi largement répandu dans toutes les industries, l'air comprimé est parfois considéré comme étant le "quatrième service public".
Dans de nombreuses installations, les systèmes d'air comprimé constituent les équipements présentant la plus basse efficacité énergétique. Il existe donc d'innombrables possibilités de mettre en œuvre des programmes d'efficacité énergétique pour ces systèmes.
Par le passé, une pratique courante dans la prise de décisions concernant les équipements à air comprimé et les utilisations finales, consistait à se baser sur la notion de coût de revient de base. Or, pour établir le rendement optimal d'un système, on doit tenir compte des coûts actualisés de l'énergie, de la productivité et de l'entretien. En d'autres mots, les meilleures pratiques de prise de décisions doivent se fonder sur le coût global du cycle de vie du système d'air comprimé et de ses composantes.
Pour améliorer et conserver l'optimisation d'un système d'air comprimé, il faut donc analyser à la fois le côté production et le côté consommation du système, et bien comprendre leurs interactions.
La gestion appropriée d'un système d'air comprimé aide non seulement à réaliser des économies d'électricité, mais aussi à réduire les périodes d'indisponibilité, accroître la productivité, diminuer l'entretien, et enfin améliorer la qualité des produits.
Un rendement optimal est réalisable en spécifiant et en dimensionnant les équipements de façon appropriée, en faisant fonctionner le système à la plus basse pression possible, en arrêtant les appareils inutiles et en prêtant attention aux dispositifs de régulation du compresseur et aux installations de stockage de l'air comprimé. La réparation des fuites d'air chroniques entraînera par ailleurs une réduction additionnelle des coûts.
Dans l'exemple d'une application type utilisant de l'air comprimé, comme un moteur pneumatique ou une pompe à membrane, le compresseur va consommer environ 10 unités d'énergie électrique pour produire environ une unité mécanique de travail réel.
C'est pourquoi avant d'employer des appareils entraînés par l'air comprimé, il convient d'envisager au préalable d'autres méthodes d'utilisation de l'énergie, comme par exemple des moteurs électriques à entraînement direct. Lorsqu'une application donnée exige de l'air comprimé, elle doit en principe utiliser la quantité d'air et la pression nécessaires les plus faibles, et ce pour une durée la plus courte possible. L'usage de l'air comprimé devra également être surveillé et réévalué en permanence.
Types de compresseurs d’air et dispositifs de régulation
Il existe en gros deux types fondamentaux de compresseurs :
- Les compresseurs volumétriques
- Les compresseurs dynamiques.
Compresseurs volumétriques.
Dans le type volumétrique, une quantité donnée d'air est aspirée dans une chambre de compression puis le volume que l'air occupe est diminué, ce qui entraîne une augmentation correspondante de sa pression avant qu'il soit refoulé. Les compresseurs d'air rotatifs à vis, les compresseurs à palettes et les compresseurs à pistons sont les trois types les plus répandus de compresseurs volumétriques utilisés dans les petites et moyennes industries.
Compresseurs dynamiques.
Les compresseurs d'air dynamiques, qui comprennent des machines centrifuges et des machines axiales, sont courants dans les très grosses installations de fabrication. Ces compresseurs sortent du cadre du présent document.
Compresseurs rotatifs à vis
Depuis les années 1980, les compresseurs rotatifs à vis connaissent une certaine popularité et ont conquis une part intéressante du marché (par rapport aux compresseurs à pistons). Ils sont les plus répandus pour des puissances comprises entre 5 et 900 HP. Le type le plus courant de compresseur rotatif est le compresseur à vis à deux rotors hélicoïdaux. Deux rotors accouplés sont engrainés ensemble, emprisonnant l'air et réduisant son volume le long des rotors. Selon les exigences de pureté de l'air, les compresseurs rotatifs à vis sont du type lubrifié ou sec (sans huile.
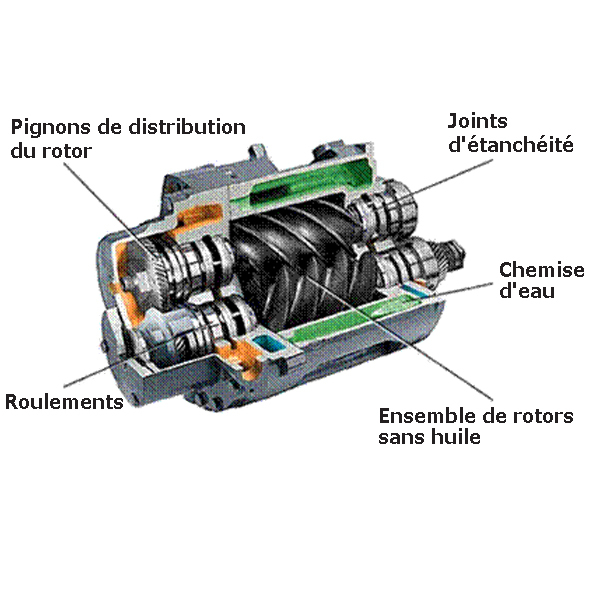
Version texte
Figure 6 - Coupe d'un compresseur rotatif à vis type
arrachée illustration montrant pignons de distribution de rotor, joints, chemise d'eau, sans huile tournent ensemble, et les roulements.
Figure 6 - Coupe d'un compresseur rotatif à vis type
(avec la permission de Atlas Copco)
L'avantage majeur des compresseurs à vis par rapport aux compresseurs à pistons de petite puissance refroidis par air est qu'ils peuvent tourner sans interruption à pleine charge, alors que les compresseurs à piston doivent être employés avec un facteur d'utilisation maximal de 60 %. Les compresseurs rotatifs à vis sont en outre bien plus silencieux et produisent de l'air plus froid qu'il est plus facile de sécher. Sachez toutefois que les compresseurs rotatifs à vis peuvent ne pas être le meilleur choix en matière d'efficacité comparativement aux compresseurs à pistons à régulation tout ou rien. Reportez- vous à l'exemple du Cas 3: régulation tout ou rien comparée à régulation en charge/à vide à la page 48.
Compresseur rotatif à vis à injection d'huile. Le compresseur rotatif à vis à injection d'huile constitue le type le plus répandu de compresseur industriel pour de nombreuses applications. Le lubrifiant employé dans ce type de compresseurs peut être soit à base d'hydrocarbures, soit un produit synthétique. En principe, la sortie d'air comprend un mélange d'air comprimé et de lubrifiant injecté et passe par un carter dans lequel le lubrifiant est extrait de l'air comprimé. Des changements de direction et de vitesse permettent de séparer la plus grande partie du liquide. Les aérosols résiduels dans l'air comprimé sont alors séparés dans un élément de séparation situé à l'intérieur du carter et il ne subsiste dans l'air comprimé que quelques parties par million (ppm) de lubrifiant.
Dans le cas des compresseurs à deux étages, le refroidissement entre étages et les pertes internes minimes en raison de la pression plus faible dans chaque étage, augmentent l'efficacité du processus de compression. Par suite, la compression de l'air à la pression finale demande moins d'énergie.
Compresseur rotatif à vis sec. Dans ce type de compresseur exempt d'huile, les rotors engrenants ne sont pas en contact, des engrenages de synchronisation extérieurs maintenant le jeu qui les sépare dans des tolérances très faibles. Dans la plupart des modèles, on emploie deux étages de compression avec refroidisseur intermédiaire et refroidisseur de sortie. Les compresseurs rotatifs à vis exempts d'huile existent dans une gamme de 25 à 1200 HP ou de 90 à 5200 pcm.
Compresseurs à pistons
Les compresseurs de ce type comportent un piston entraîné par un vilebrequin et un moteur électrique. Les compresseurs à piston à usage général sont disponibles sur le marché dans des puissances comprises entre moins de 1 HP et 30 HP environ. Ils sont souvent employés pour fournir de l'air à des dispositifs de régulation et d'automatisation dans les bâtiments.
On trouve encore dans l'industrie des compresseurs à pistons de grande puissance, mais ils ne sont plus commercialisés aujourd'hui sauf pour des procédés spécialisés tels que les applications à haute pression.
Compresseurs à palettes
Un compresseur rotatif à palettes met en jeu un rotor à rainures excentré, situé dans un cylindre. Les rainures longitudinales du rotor sont équipées chacune d'une palette. Lorsque le rotor tourne, ces palettes sont plaquées vers l'extérieur par la force centrifuge et elles coulissent à l'intérieur des rainures en raison de l'excentricité du rotor par rapport au stator. Les palettes balayent le cylindre, aspirant l'air d'un côté et le rejetant de l'autre. Les compresseurs à palettes servent généralement dans des applications de petite puissance lorsqu'existent des problèmes d'encombrement; ils ne sont toutefois pas aussi efficaces que les compresseurs rotatifs à vis.
Moteurs de compresseurs
Les moteurs électriques constituent le moyen le plus courant d'entraînement des compresseurs. En tant que moteurs d'entraînement, ils doivent délivrer une puissance suffisante pour démarrer le compresseur, l'accélérer jusqu'à sa pleine vitesse, et assurer son fonctionnement dans les diverses conditions prévues. La plupart des compresseurs d'air utilisent des moteurs électriques triphasés à induction classiques.
Pour les compresseurs d'air neufs ou de remplacement, on devra spécifier des moteurs à haut rendement certifiés Premium plutôt que des moteurs standards. Le coût marginal d'un moteur à haut rendement certifié Premium est en général amorti rapidement en raison des économies d'énergie qu'il procure.
Pour de plus amples informations en ce qui concerne les moteurs à haut rendement, veuillez vous reporter au Guide de référence sur l'efficacité énergétique des moteurs publié par CEATI.
Dispositifs de régulation des compresseurs et rendement des systèmes
Vu que les systèmes d'air comprimé fonctionnent rarement à leur pleine puissance en permanence, il est essentiel de pouvoir en contrôler le débit avec précision sous des charges partielles.
On devra tenir compte à la fois du choix du compresseur ET de celui des dispositifs de régulation du système, car ce sont des éléments importants et qui influent sur le rendement du système et sur son efficacité énergétique.
- Mode tout ou rien. Il s'agit de la stratégie de régulation la plus simple et la plus efficace. Elle s'applique tant aux compresseurs à piston qu'aux compresseurs rotatifs à vis. Son principe est le suivant : le moteur entraînant le compresseur est mis en marche ou arrêté en fonction de la pression de refoulement de la machine. Dans ce mode, un pressostat délivre le signal marche/arrêt du moteur. Les stratégies de régulation tout ou rien conviennent généralement aux compresseurs d'une puissance inférieure à 30 HP.
Des démarrages répétés peuvent conduire à une surchauffe du moteur et exiger un plus grand entretien des composantes du compresseur. C'est pour cela que le dimensionnement des réservoirs de stockage et le maintien de larges plages de prèssion de fonctionnement devront faire l'objet d'une attention particulière, de façon à maintenir le nombre de démarrages du moteur dans des limites acceptables.
- Mode en charge/à vide. Ce mode de régulation est parfois nommé régulation directe/indirecte. Le moteur fonctionne en permanence, mais le compresseur est délesté lorsque la pression de refoulement est appropriée. Les compresseurs rotatifs à vis fonctionnant à vide consomment de 15 à 35 % de leur puissance absorbée en charge, alors qu'ils ne produisent pas d'air comprimé. Des minuteries de délestage facultatives permettent d'économiser de l'énergie en arrêtant automatiquement le compresseur et en le gardant en réserve s'il fonctionne à vide pendant une période de temps donnée (normalement 15 minutes).
Pour parvenir à un bon rendement du fonctionnement sous charge partielle, les modes de régulation en charge/à vide nécessitent des réservoirs de régulation de grande capacité.
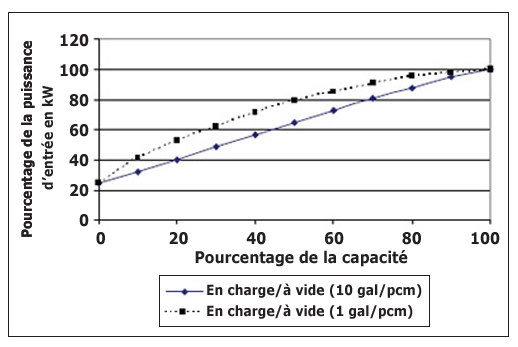
Version texte
Pourcentage de la puissance d'entrée en kw | Pourcentage de la capacité (En charge/à vide 1 gal/pcm) | Pourcentage de la capacité (En charge/à vide 10 gal/pcm) |
---|---|---|
0% | 25% | 25% |
20% | 55% | 40% |
40% | 70% | 58% |
60% | 85% | 75% |
80% | 95% | 90% |
100% | 100% | 100% |
Figure 7 - Puissance moyenne contre capacité d'un compresseur rotatif à vis avec régulation en charge/à vide et variation de la capacité du réservoir (avec la permission de Compressed Air Challenge)
- Régulation par modulation. Ce mode de régulation fait varier le débit du compresseur pour répondre à la demande en réglant la vanne d'aspiration, réduisant ainsi l'entrée d'air du compresseur. Même dans le cas où ils sont modulés pour un débit nul, les compresseurs rotatifs à vis consomment environ 70 % de leur consommation à pleine charge. L'emploi de dispositifs de régulation de délestage actionnés par pressostats peut réduire la consommation de fonctionnement à vide entre 15 et 35 % de la consommation à pleine charge. La régulation par modulation est spécifique aux compresseurs à vis lubrifiés et constitue la méthode la moins efficace de les faire fonctionner.
Les dispositifs de régulation des compresseurs ont un effet marqué sur leur consommation d'énergie, notamment dans le cas des faibles débits pour lesquels les régulations tout ou rien offrent en général le meilleur rendement énergétique.
La Figure 8 montre une courbe de rendement type de compresseurs commandés par modulation de la vanne d'aspiration avec et sans délestage du compresseur.
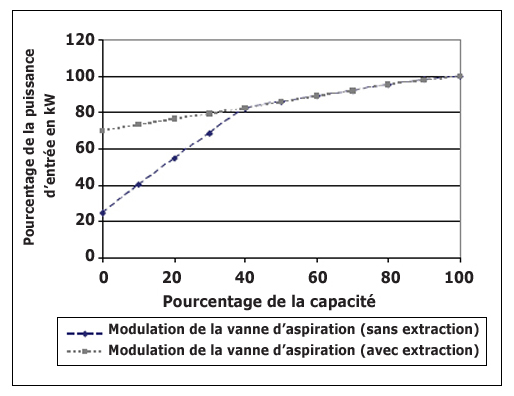
Version texte
Pourcentage de la puissance d'entrée en kw | Pourcentage de la capacité (Modulation de la vann d'aspiration - sans extraction) | Pourcentage de la capacité (Modulation de la vann d'aspiration - avec extraction) |
---|---|---|
0% | 25% | 70% |
20% | 55% | 75% |
40% | 82% | 82% |
60% | 90% | 90% |
80% | 95% | 95% |
100% | 100% | 100% |
Figure 8 - Compresseur rotatif à vis commandé par modulation de la vanne d'aspiration (avec la permission de Compressed Air Challenge)
- Compresseurs à cylindrée variable. Certains modèles de compresseurs rotatifs à vis lubrifiés ont un débit de sortie variable qui est obtenu à l'aide de vannes de régulation spéciales, également appelées vannes à spirale, tournantes ou à clapet. Grâce à un système de régulation de la cylindrée variable, la pression de sortie et la consommation d'énergie du compresseur peuvent être très bien commandées sans avoir à démarrer/arrêter ou mettre en charge/ délester le compresseur. Ce mode de régulation offre un rendement satisfaisant pour des points de fonctionnement supérieurs à 60 % de la charge. Pour des débits inférieurs à 40 % de la capacité, l'utilisation de régulation de délestage par pressostats peut fortement réduire la consommation en énergie dans le cas des débits plus faibles.
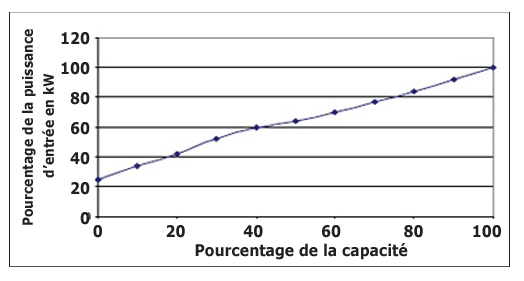
Version texte
Pourcentage de la puissance d'entrée en kw | Pourcentage de la capacité |
---|---|
0% | 25% |
20% | 40% |
40% | 60% |
60% | 70% |
80% | 80% |
100% | 100% |
Figure 9 - Compresseur rotatif à vis à cylindrée variable (avec la permission de Compressed Air Challenge)
- Entraînement à vitesse variable (VSD).
Dans ce mode de régulation, on fait varier la vitesse du compresseur en fonction des variations de la demande en air comprimé. On peut acheter des compresseurs à vis, lubrifiés ou non, avec des dispositifs de régulation de variation de la vitesse qui adaptent en continu la vitesse du moteur d'entraînement aux variations de la demande et assurent le maintien d'une pression constante. Normalement, ces types de compresseurs fonctionnent en régulation tout ou rien ou en charge/à vide lorsque la demande d'air comprimé tombe à une valeur inférieure à celle correspondant à la vitesse minimale de l'entraînement.
La plupart du temps, les compresseurs à vitesse variable offrent le meilleur rendement de fonctionnement à charge partielle. Théoriquement, lorsqu'une installation comporte de multiples compresseurs d'air, un ou plusieurs compresseurs à vitesse fixe devraient assurer la demande de base en air comprimé, un compresseur à vitesse variable (VSD) répondant alors aux demandes d'air variables ou momentanées.
Pour tirer pleinement parti des compresseurs à vitesse variable, on doit évaluer le volume approprié des réservoirs de stockage d'air pour différents scénarios de débit et de régulation.
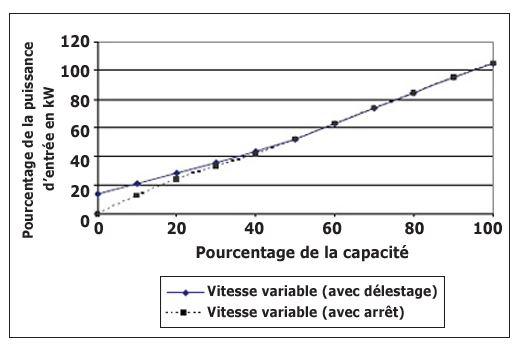
Version texte
Pourcentage de la puissance d'entrée en kw | Pourcentage de la capacité (vitesse variable - avec délestage) | Pourcentage de la capacité (variable speed - avec arrêt) |
---|---|---|
0% | 15% | 0% |
20% | 30% | 25% |
40% | 42% | 42% |
60% | 60% | 60% |
80% | 85% | 85% |
100% | 105% | 105% |
Figure 10 - Courbe d'un compresseur rotatif à vis à vitesse variable en supposant des pertes de 5 % dans l'onduleur (avec la permission de Compressed Air Challenge)
Il convient d'envisager des compresseurs à vitesse variable (VSD) pour répondre aux demandes momentanées (ou aux fluctuations de la demande), car ce sont en principe les compresseurs les plus efficaces pour alimenter des charges partielles.
Aptes à fournir de l'air à pression constante dans une gamme étendue de régulation, les compresseurs VSD ont une consommation d'énergie et un débit qui sont presque directement proportionnels à leur vitesse. Il pourrait ainsi en découler des économies d'énergie par rapport aux compresseurs à vitesse fixe comparables au cas où les compresseurs fonctionnent sous charge partielle. Souvenez-vous toutefois qu'aux pleines charges, les compresseurs VSD vont consommer légèrement plus d'énergie que les compresseurs à entraînement par moteur à vitesse constante de puissance comparable.
Comparaison des coûts de fonctionnement des différents modes de régulation
Le mode de régulation d'un compresseur peut avoir un effet prononcé sur ses coûts de fonctionnement. En mode de modulation, le compresseur va utiliser 90 % de sa puissance nominale. En mode en charge/à vide avec une capacité de stockage d'air minimale (1 gallon US par pi³), le compresseur va consommer environ 92 % de sa puissance nominale. En portant la capacité de stockage de l'air à 10 gallons US par pi³, le compresseur en mode en charge/à vide va consommer environ 77 % de sa puissance nominale. Équipé d'un dispositif de régulation à vitesse variable, le même compresseur va consommer environ 66 % de sa puissance nominale.
présente les coûts de fonctionnement pour un compresseur de 100 HP fonctionnant à 65 % de la charge moyenne.
% de la charge | Modulation | En charge/à vide avec réservoir de 1 gal/pi³ |
En charge/à vide avec réservoir de 10 gal/pi³ |
Entraînement à vitesse variable |
---|---|---|---|---|
100 | 36 130 $ | 36 130 $ | 36 130 $ | 36 850 $ |
75 | 33 420 $ | 34 680 $ | 29 350 $ | 27 090 $ |
65 | 32 330 $ | 33 240 $ | 27 820 $ | 23 480 $ |
50 | 30 710 $ | 31 070 $ | 24 200 $ | 18 060 $ |
25 | 28 000 $ | 24 930 $ | 16 800 $ | 9 030 $ |
10 | 26 370 $ | 16 620 $ | 11 740 $ | 3 610 $ |
* Sur la base de 10 cents par kWh et de 4 250 heures par an.
Dispositifs de régulation de système de compresseurs multiples
Dans les systèmes de régulation de compresseurs multiples, le but recherché est de maintenir automatiquement, dans toutes les conditions de débit, la pression la moins élevée et la plus constante possible, tout en assurant que tous les compresseurs en service, à l'exception d'un seul, fonctionnent à pleine charge ou sont arrêtés. Le compresseur d'exception (unité d'appoint) devrait être celui qui est le plus apte à fonctionner avec un bon rendement aux charges partielles.
Les régulations locales du compresseur maintiennent de façon indépendante l'équilibre entre le débit du compresseur et la demande du système d'air comprimé et font toujours partie intégrante du compresseur. Pour atteindre le but recherché dans la régulation de compresseurs multiples, on doit faire appel à des dispositifs ou des modes de régulation plus sophistiqués (plages de pression en cascade, régulation supérieure en réseau ou du système) afin de coordonner le fonctionnement des compresseurs et la fourniture de l'air comprimé au système.
Dans un système d'air comprimé à compresseurs multiples, il est indispensable d'assurer une coordination appropriée qui permette de maintenir une pression adéquate et une efficacité accrue dès que plusieurs compresseurs sont appelés à fonctionner.
Du fait que les systèmes de compresseurs sont généralement dimensionnés pour répondre à la demande maximale d'une installation, mais qu'ils fonctionnent normalement à des charges partielles, il est indispensable qu'une méthode de régulation garantisse que les compresseurs en marche fonctionnent avec une efficacité maximale. Voici une description de quelques méthodes courantes de régulation :
- Régulation par plages de pression en cascade. Ce type de régulation est la méthode la plus simple pour coordonner des compresseurs multiples. Dans ce mode de régulation, les pressostats de régulation locale des compresseurs sont réglés selon une configuration de chevauchement ou en cascade (voir la Figure 12). Cette méthode de régulation va mettre à vide ou en charge les compresseurs pour différentes valeurs de la pression dans le système, à mesure que la charge diminue ou augmente. La méthode de régulation en cascade se traduit par des pressions du système plus élevées que nécessaire pendant les périodes de charge partielle, ce qui occasionne une consommation d'énergie trop élevée. Par ailleurs, à mesure que le nombre de compresseurs à coordonner augmente, il devient de plus en plus difficile d'assurer une régulation précise des compresseurs sans dépasser, lors des faibles charges, la pression nominale des compresseurs raccordés au système, ou sans éprouver une pression basse dans le système pour les charges élevées.
Version texte
Figure 12 - Régulation en cascade d'un ensemble de compresseurs multiples;
compresseur #1 fonctionne avec une pression du système (psig) de 100 à 110 psig;
compresseur #2 fonctionne avec une pression du système (psig) de 95 à 105 psig;
compresseur #3 fonctionne avec une pression du système (psig) de 90 à 100 psig;
compresseur #4 fonctionne avec une pression du système (psig) de 85 à 95 psig;Figure 12 - Régulation en cascade d'un ensemble de compresseurs multiples
(avec la permission de Compressed Air Challenge) - Régulation en réseau. Ce type de régulation fait appel à une caractéristique optionnelle de la régulation locale du compresseur pour le mettre en communication avec les autres compresseurs et former ainsi une chaîne de communication qui prend les décisions de marche/arrêt, mise en charge/délestage, modulation et variation de la vitesse. En général, un des compresseurs assure le rôle de chef de file alors que les autres sont asservis aux instructions du premier. Ce type de régulation est adaptable à un grand nombre de compresseurs tout en maintenant la pression dans le système, dans une plage de pressions plus faibles pour toutes les conditions de débit. En principe ce type de régulation ne peut interconnecter que des compresseurs du même fabricant.
- Dispositifs de régulation supérieure des systèmes. (Également appelés séquenceurs automatiques). Comparables aux dispositifs de régulation en réseau, ces dispositifs de régulation externes sont reliés au contrôleur local de chaque compresseur et permettent de maintenir la pression d'air comprimé du système dans une seule plage de pression plus étroite. La plupart des dispositifs de régulation supérieure peuvent s'adapter à des compresseurs de marques et types différents dans un même système d'air comprimé. Certain des dispositifs les plus récents comportent un grand nombre de fonctionnalités supplémentaires dont la possibilité de surveillance et de régulation des paramètres importants du système.
- Régulation multiple de compresseurs VSD. Les modes de régulation décrits plus haut peuvent englober un ou plusieurs compresseurs VSD. Il est alors important de s'assurer que la puissance variable totale est égale ou supérieure à celle du compresseur à vitesse fixe le plus puissant, à défaut de quoi il en résultera des lacunes dans la régulation. Une lacune de régulation intervient lorsque, dans certaines conditions, la charge du système ne peut être satisfaite ni par la puissance de base, ni par celle des compresseurs VSD. Cette lacune de régulation va provoquer un conflit entre compresseurs de base et compresseurs VSD pour la position maîtresse, ce qui abaissera l'efficacité du système. Votre fournisseur pourra vous aider en termes de dimensionnement adéquat de vos compresseurs VSD.
Afin de tirer plein parti de la régulation de compresseurs multiples, il faut installer un volume approprié de réservoirs de stockage d'air de façon à freiner les variations de pression dans le système et à disposer du temps nécessaire au démarrage et à l'arrêt des compresseurs VSD. Le stockage est un élément plus important dans le cas de la régulation de type en charge/à vide, mais il est également nécessaire dans le cas des systèmes équipés de compresseurs VSD.
Équipements auxiliaires des compresseurs d’air
Les équipements auxiliaires des compresseurs d'air incluent les refroidisseurs de sortie, filtres, séparateurs, sécheurs, récupérateurs de chaleur, dispositifs de lubrification, régulateurs de pression, réservoirs d'air, purgeurs de condensats et dispositifs de purge automatiques. Ce sont des dispositifs connexes d'un compresseur d'air qui contribuent à conditionner l'air comprimé selon les spécifications imposées.
Refroidisseurs de compresseurs d'air
Environ 80 pour cent de l'énergie électrique consommée par un compresseur est transformée en chaleur. Comme option d'un programme d'efficacité énergétique, la chaleur due à la compression peut être récupérée et utilisée pour chauffer de l'eau ou de l'air. La récupération de la chaleur des compresseurs d'air constitue une excellente possibilité d'efficacité énergétique dans bon nombre d'installations.
Refroidissement des compresseurs. Les compresseurs qui fonctionnent en permanence engendrent d'importantes quantités de chaleur attribuable au processus de compression. Cette chaleur doit être extraite à la fois du refroidisseur d'air de sortie et du refroidisseur d'huile. Les compresseurs sont normalement refroidis par air ou par eau.
- Refroidisseurs intermédiaires. De nombreux compresseurs anciens à plusieurs étages sont équipés de refroidisseurs intermédiaires qui sont chargés d'éliminer, entre chaque étage, la chaleur de compression. Ces refroidisseurs doivent être nettoyés périodiquement afin d'assurer une capacité optimale de transfert de chaleur aux fin d'une meilleure efficacité énergétique.
- Refroidisseurs de sortie. Ces refroidisseurs extraient la chaleur du lubrifiant et de l'air de refoulement du compresseur. Le refroidisseur d'air, installé en aval du dernier étage de compression, est refroidi par air ou par eau. Il est essentiel de veiller à son bon fonctionnement car la teneur en humidité de l'air dépend directement de la température de refoulement. Ces refroidisseurs d'air doivent être nettoyés régulièrement pour assurer une capacité optimale de transfert de chaleur aux fins d'une meilleure efficacité énergétique. Des températures supérieures à 38 °C provoquent généralement une surcharge des sécheurs d'air et entraînent des problèmes d'humidité. Les refroidisseurs réduisent la température de l'air de refoulement saturé et condensent la vapeur d'eau qui doit alors être séparée et vidangée du système. L'entretien du dispositif de purge est essentiel si l'on veut éviter que de l'eau libre ne pénètre dans les équipements de séchage avals. Pratiquement tous les systèmes d'air comprimé industriels sont équipés d'un type ou un autre de refroidisseurs de sortie.
- Entrée d'air du compresseur. On admet en général, bien que cette idée fasse encore l'objet de débats dans l'industrie, que pour une efficacité énergétique maximale, l'air entrant dans le compresseur doit être le plus froid possible. Ceci tient au fait que l'air froid est plus dense que l'air chaud. Plus l'air d'entrée est froid, plus ses molécules le sont également, de sorte que davantage d'air est comprimé pour chaque tour du compresseur d'air. En outre, plus l'air d'entrée est froid, moins il y a nécessité de refroidissement intermédiaire et de refroidissement de sortie.
Un compresseur dont l'entrée d'air est alimentée par de l'air extérieur (au lieu de l'air très chaud existant dans une salle de compresseurs) a une meilleure efficacité énergétique. Lors de la conception des prises d'air extérieures, on devra prendre en compte la pression différentielle, le gel et les blocages par le givre en hiver, en vue d'optimiser les économies d'énergie. Qui plus est, les salles de compresseurs devront être aussi propres et fraîches qu'il est possible afin d'assurer un fonctionnement optimal des compresseurs.
Sécheurs d'air
L'air comprimé quittant le refroidisseur de sortie et le séparateur d'humidité d'un compresseur est en principe plus chaud que l'air ambiant et complètement saturé d'humidité. À mesure que l'air se refroidit, la vapeur se condense dans les canalisations d'air comprimé. Une quantité excessive d'humidité entraînée risque d'aboutir à des effets indésirables tels que corrosion des tuyauteries et contamination au point final d'utilisation. C'est cette raison qui justifie l'installation d'un sécheur d'air.
Les divers types de sécheurs d'air comprimé possèdent différentes caractéristiques de fonctionnement et permettent d'obtenir différents écarts de température par rapport au point de rosée (le point de rosée est la température à laquelle l'humidité se condense dans l'air).
Certaine utilisations finales exigent un air très sec, comme par exemple les systèmes de distribution d'air comprimé dans lesquels les tuyauteries sont exposées à des conditions hivernales. Pour éviter la formation de givre, on doit procéder au séchage de l'air à un point de rosée inférieur à la température ambiante.
La perte de charge type entre l'entrée et la sortie d'un sécheur d'air comprimé est de l'ordre de 3 à 5 psi. Certains sécheurs d'installations industrielles sont sous-dimensionnés et provoquent des pertes de charge encore plus élevées. Pour une efficacité énergétique constante, l'air ne devrait être séché qu'au point de rosée voulu et au moyen d'un sécheur de taille appropriée.
Les sécheurs d'air s'inscrivent dans trois grandes catégories : à réfrigération, à régénération et à membrane.
Sécheurs à réfrigération. Parmi les principaux types de sécheurs à réfrigération, on peut citer :
- Sécheurs à réfrigération à fonctionnement continu (également appelés à détente directe). Ce type de sécheur d'air est le plus répandu en raison de son coût initial relativement faible. Il convient aux systèmes pouvant fonctionner à des points de rosée supérieurs à 2 °C. Le sécheur d'air abaisse le point de rosée de l'air à la température approximative de l'air sortant de l'évaporateur du frigorigène. Pour éviter le givrage à l'intérieur du sécheur, la température de l'évaporateur ne devrait pas descendre en dessous de 0 °C. Compte tenu du rendement du sécheur, on obtiendra en général un point de rosée d'air sous pression de 2 °C ou plus pour l'air quittant le sécheur.
Après que l'air ait d'abord traversé un échangeur de chaleur qui transfère la chaleur de l'air entrant à l'air sortant plus froid, le sécheur d'air abaisse le point de rosée de l'air jusqu'à la température approximative de l'air quittant l'évaporateur du frigorigène. Ceci provoque la condensation de la vapeur d'eau qui est ensuite éliminée dans le séparateur du sécheur. Pour éviter le givrage à l'intérieur du sécheur, la température de l'évaporateur est normalement réglée à l'aide d'un clapet de dérivation des gaz chauds qui oblige le frigorigène à contourner l'évaporateur. Cette dérivation maintient chargé le compresseur de frigorigène, forçant le sécheur à fonctionner à pratiquement sa pleine puissance même lorsque sa charge est faible, aboutissant ainsi à une efficacité médiocre en charge partielle.
On peut réaliser des économies d'énergie en mettant le sécheur d'air à l'arrêt pendant les heures où le compresseur est lui-même arrêté.
- Sécheurs à réfrigération à fonctionnement cyclique (on dit également à masse thermique). Ces sécheurs ont les mêmes caractéristiques de point de rosée que les sécheurs à réfrigération à fonctionnement continu, mais au lieu d'un clapet de dérivation des gaz chauds pour commander la température de l'évaporateur, on utilise une masse thermique pour accumuler le froid. Ceci permet au compresseur de frigorigène de fonctionner en mode tout ou rien sans cycles superflus. Le sécheur à fonctionnement cyclique offre une très bonne marge de réglage effective en réaction aux diminutions de débit et du taux d'humidité, ce qui se traduit par une bonne efficacité à charge partielle.
- Sécheurs à réfrigération à vitesse variable. Dans ce type de sécheur, la capacité de séchage est adaptée à la demande du système à l'aide de dispositifs électroniques, ce qui leur confère une bonne efficacité à charge partielle.
Sécheurs à régénération. Ce type de sécheur à adsorption fait appel à un matériau poreux pour sécher l'air. Lorsqu'il devient saturé, le matériau déshydratant doit être régénéré. Selon leur conception, les sécheurs régénérateurs emploient différentes méthodes de régénération. Ces sécheurs permettent d'éliminer l'humidité jusqu'à des seuils très inférieurs au point de congélation de l'eau ( 40 °F ou 0 °C, ou même moins). Toutefois, la consommation d'air de purge pour la régénération du sécheur risque de pénaliser fortement le système au niveau de l'énergie consommée.
Il existe des dispositifs de régulation du point de rosée qui ajustent les besoins en énergie de régénération à la demande du système d'air comprimé. L'emploi de ces dispositifs permettra d'améliorer l'efficacité énergétique du sécheur.
Les principales catégories de sécheurs à régénération incluent :
- Régénération sans chaleur. Ce type de sécheur fait appel à l'air séché déjà comprimé pour régénérer le matériau déshydratant. Un sécheur d'air sans chaleur non régulé va consommer en permanence entre 15 et 20 % de sa puissance nominale pour effectuer cette opération. Il en coûtera près de 3 à 4 kW par 100 pcm de puissance nominale du sécheur.
- Régénération avec purge. Ce type de sécheur consomme un plus faible pourcentage (7 %) d'air déjà comprimé émanant du système et lui fait traverser des résistances chauffantes électriques. L'air réchauffé extrait de façon plus efficace l'humidité du matériau déshydratant du sécheur. Ce type de sécheur consomme près de 2,25 kW par 100 pcm de puissance nominale du sécheur.
- Régénération avec purge par balayage. Dans ce type de sécheurs, une soufflante fait passer l'air ambiant réchauffé à travers le matériau déshydratant pour le régénérer. Vu que cette opération ne consomme aucun air comprimé, la puissance de sortie du compresseur reste entièrement utilisable par le système d'air comprimé. Au terme du cycle de chauffage, le refroidissement s'effectue par air comprimé. Ces appareils consomment environ 2,5 kW par 100 pcm de puissance nominale du sécheur. Lorsqu'elle est employée, la purge pour refroidissement consomme en outre 0,6 kW par 100 pcm de puissance nominale.
Sécheurs à membrane. Ces appareils utilisent une membrane semi-perméable pour séparer la vapeur d'eau du flux d'air. Ils ne comportent aucune pièce mobile. Pour le balayage de la membrane, ces sécheurs consomment près de 20 % de leur puissance nominale. L'air de balayage constitue une perte pour le système d'air comprimé. Ces sécheurs délivrent en sortie des points de rosée variables selon le débit d'air et la température.
La Figure 13 présente les coûts de fonctionnement pour les types de sécheurs courants.
% de charge | Réfrigération en continu | Réfrigération cyclique | Régénération sans chaleur | Régénération sans chaleur régulée | Sécheur à membrane |
---|---|---|---|---|---|
100 % | 1 070 $ | 1 070 $ | 6 390 $ | 6 390 $ | 8 520 $ |
75 % | 1 070 $ | 800 $ | 6 390 $ | 4 790 $ | 8 520 $ |
50 % | 1 070 $ | 530 $ | 6 390 $ | 3 200 $ | 8 520 $ |
25 % | 1 070 $ | 270 $ | 6 390 $ | 1 600 $ | 8 520 $ |
10 % | 1 070 $ | 110 $ | 6 390 $ | 640 $ | 8 520 $ |
0 | 1 070 $ | 0 $ | 6 390 $ | 0 $ | 8 520 $ |
*Sur la base d'un sécheur d'une capacité de 500 pcm fonctionnant 4 250 heures par an à 100 psi (lb/po²) et de 10 ¢/kWh.
Outre les coûts d'énergie et d'immobilisation de matériel, il faut tenir compte du fait que le séchage de l'air à -40°C coûte de 5 à 10 fois plus cher que le séchage à +2°C.
Filtres
Filtre d'admission d'air du compresseur. Un filtre d'admission d'air protège le compresseur contre les particules, insectes et matériaux végétaux qui se trouvent en suspension dans l'air.
Les filtres d'admission d'air doivent être périodiquement remplacés, notamment dans les zones où prédominent poussières et insectes. Un filtre d'entrée à pression différentielle élevée diminue la capacité de refoulement d'un compresseur d'air et réduit son efficacité.
Filtres à air comprimé. On doit généralement installer des filtres à air comprimé en aval du compresseur d'air pour éliminer les impuretés telles que particules, condensats et huile. De nombreux choix de méthodes de filtration existent qui dépendent de la propreté exigée pour l'air.
De façon générale, la pression différentielle dans un filtre est d'autant plus élevée que le filtre est plus fin. Les filtres à particules servant à éliminer les particules solides présentent la pression différentielle la plus faible.
Les filtres à coalescence employés pour éliminer l'huile et l'humidité ont généralement la pression différentielle la plus élevée. Des filtres à particules sont ordinairement utilisés immédiatement en aval d'un sécheur à adsorption pour éliminer les particules de matériau déshydratant.
La pression différentielle d'un filtre croît comme le carré de l'augmentation du débit qui le traverse. Cette différence de pression due au filtre augmente la consommation d'énergie du compresseur nécessaire pour obtenir une pression de sortie donnée.
Pour chaque augmentation de 2 psi de la pression différentielle dans un filtre, il faut compter une augmentation de 1 % des coûts en énergie. Si l'on double la capacité d'un filtre donné, la perte de pression à travers ce filtre va être réduite dans un rapport de 4 à 1, ce qui correspond à une économie d'énergie de 75 %. Du point de vue efficacité énergétique, on devra choisir avec soin les types de filtres car l'excès de filtration représente une perte d'énergie.
Pour les filtres à huile et à particules, n'employer que le niveau de filtration nécessaire à chaque application. La pression différentielle des filtres doit être soigneusement surveillée et les éléments de filtres remplacés selon les instructions du fabricant, où lorsque la différence de pression entraîne une consommation d'énergie excessive. La différence de pression devra être surveillée à l'aide d'indicateurs de pression différentielle précis.
Pour économiser de l'énergie, tenter de minimiser - lorsqu'il est possible - la chute de pression dans les filtres en installant des filtres du type éliminateurs de gouttelettes à faible pression différentielle, des filtres surdimensionnés, ou en employant des filtres montés en parallèle.
Il faut garder à l'esprit que des différentiels de pression de filtres trop élevés entraînent souvent une consommation plus élevée du compresseur en raison du fonctionnement en cycles courts de ce dernier.
Exemple 1 - Coût de filtres colmatés
Prenons par exemple un compresseur de 100 HP fonctionnant durant 2 quarts de travail et dont la pression de refoulement est fixée à 100 psi (lb/po²). Le coût annuel en électricité de ce compresseur s'élève à 32 330 $ (voir Figure 4). Si cet appareil devait fonctionner à une pression de 110 psi pour compenser un différentiel total de filtres de 10 psi, il en résulterait une perte d'énergie d'environ 5 % ou 1 615 $ annuellement. Dans la plupart des cas, une conception adéquate peut réduire la pression différentielle à moins de 1 psi.
Réservoirs et stockage de l'air comprimé
L'existence de réservoirs de stockage d'une capacité adéquate permet de préserver la qualité de l'air, la stabilité du système d'air comprimé, ainsi que son efficacité. Un stockage d'air approprié est une chose extrêmement importante dans un système où sont employés des compresseurs à vis.
Les réservoirs peuvent être du type primaire ou secondaire comme on va le voir ci-dessous.
Réservoirs d'air primaires
Un réservoir d'air primaire sert de stockage général pour le système et on l'installe habituellement à proximité des compresseurs d'air principaux. Il peut se trouver en amont et/ou en aval des équipements de nettoyage.
Dans les systèmes d'air comprimé, les réservoirs d'air primaires remplissent plusieurs fonctions importantes :
- Ils amortissent les pulsations engendrées par les compresseurs à pistons.
- Ils offrent un emplacement pour la décantation de l'eau libre et de l'huile contenues dans le flux d'air comprimé.
- Ils alimentent les demandes de pointe à partir de l'air emmagasiné sans qu'il soit nécessaire de démarrer un compresseur supplémentaire.
- Ils diminuent la fréquence des cycles à vide/en charge ou marche/arrêt assurant un fonctionnement plus efficace des compresseurs à vis et réduisant les démarrages de moteurs. La plupart des compresseurs à vis comportent un dispositif de protection interne interdisant plus de 4 à 6 démarrages par heure.
- Ils ralentissent les variations de pression du système pour permettre une meilleure régulation des compresseurs et pour assurer des pressions plus stables dans le système d'air comprimé.
Une règle empirique applicable aux compresseurs à vis lubrifiés fonctionnant en mode à vide/en charge, établit que le volume des réservoirs doit être de 5 à 10 gallons US (20 à 40 litres) par pcnm de sortie de compresseur d'appoint. En termes de dimensionnement, d'autres facteurs entrent en ligne de compte : par exemple, la méthode de régulation de la capacité des compresseurs d'air et les délais de démarrage ces derniers.
L'emplacement du réservoir primaire peut avoir un impact notable sur le sécheur d'air. Les réservoirs situés en aval du sécheur d'air vont stocker d'importantes quantités d'air sec pour pouvoir répondre aux demandes de pointe. Au cas où se présente une demande soudaine dépassant la capacité du compresseur, l'air emmagasiné dans réservoir peut être utilisé directement et contribuer au maintien du débit et de la pression nécessaires. Par contre, si le réservoir primaire est situé en amont du sécheur d'air, le débit combiné du compresseur et du réservoir devra s'écouler en traversant le sécheur. Ce débit pourra, dans certains cas, dépasser la capacité du sécheur. C'est pour cela que le plus gros réservoir primaire devra être situé en aval du sécheur et des filtres.
Réservoirs d'air secondaires
Les réservoirs d'air secondaires (situés dans le système de distribution d'une installation ou aux points d'utilisation) assurent les services généraux suivants :
- Protection des utilisations finales critiques contre les creux de pression temporaires du système.
- Protection des utilisations finales multiples contre les gros utilisateurs occasionnels d'air comprimé.
- Stabilité générale de la pression dans les systèmes dont les tuyauteries de distribution sont sous-dimensionnées.
De nombreuses installations industrielles possèdent des équipements situés à l'extrémité d'une longue tuyauterie d'air comprimé, ou des machines utilisant d'importantes quantités d'air comprimé pendant de courtes périodes. Cette situation provoque souvent de sévères fluctuations de pression localisées, nombre de points finals essentiels étant alors privés d'air comprimé. Il est possible de remédier à cette situation en installant un réservoir d'air secondaire convenablement conçu à proximité du point à demande intermittente élevée. Si la demande intermittente est de courte durée, l'air nécessaire peut provenir directement du réservoir de stockage plutôt que par le démarrage d'un compresseur complémentaire. Ainsi, en installant un limiteur de débit en amont du réservoir d'air secondaire, le réservoir de stockage peut être rempli à un débit réduit raisonnable de façon à ne pas entraver les autres utilisations finales sensibles ponctuelles.
Dans d'autres cas où une utilisation isolée à faible consommation et sensible à la pression est affectée par les fluctuations de pression locales, on pourra installer un réservoir de stockage correctement dimensionné, équipé d'un clapet de non-retour et qui retiendra l'air comprimé exclusivement pour cette utilisation. De cette façon, un équipement sensible pourra rester alimenté pendant une fluctuation éventuelle de pression.
En général, un réservoir d'environ 110 gallons US (415 litres) va stocker 1 pied cubique d'air comprimé par psi (lb/po²). La taille d'un réservoir pour une application donnée est tout simplement obtenue en multipliant par 110 le nombre de pieds cubes nécessaires, et en le divisant ensuite par la plage de pression d'utilisation.
Exemple 2 - Détermination de la taille d'un réservoir d'air
Une pince pneumatique qui consomme 2 pcm nécessite un réservoir de stockage d'air muni d'un clapet antiretour permettant de maintenir au minimum une pression de 85 psi pendant 2 minutes dans un système fonctionnant normalement sous 100 psi.
- Pieds cubes nécessaires = 2 pcm × 2 minutes = 4 pieds cubes
- Plage de pression (psi) pendant l'opération =100 - 85 = 15
- Réservoir de stockage nécessaire 4 × 110/15 =29 gallons (US)
Exemple 3 - Dimensionnement d'un réservoir pour charge transitoire
Une vaste installation de décapage au jet de sable consommant 100 pcm fonctionne à raison de 1 minute toutes les 10 minutes. La décapeuse nécessite une pression de 80 psi et la pression du système d'air comprimé est de 100 psi. Sans réservoir secondaire, le système principal d'air comprimé doit fournir ce plein débit, souvent avec une pression différentielle importante dans le système. Une autre solution est d'employer un réservoir de stockage secondaire dont l'entrée est munie d'un étranglement ou d'un robinet à pointeau.
- 100 pcm x 1 minute = 100 pieds cubes
- Plage de pression (psi) = 20
- Réservoir de stockage nécessaire = 100 pieds cubes × 110/20 psi = 550 gallons (US)
- Ce réservoir pourra être rempli pendant 10 minutes à un débit de 10 pcm, ce qui réduira la pression différentielle précédente dans le système par un facteur de 100.
Pour les installations connaissant de fortes fluctuations de la demande ou ayant une pression d'air insuffisante (habituellement à l'extrémité des tuyauteries d'air), on devrait évaluer le besoin d'un ou de plusieurs réservoirs d'air situés à des emplacements stratégiques dans le système de distribution d'air comprimé.
Séparateurs et purgeurs
Les séparateurs d'eau sont des appareils qui éliminent les liquides entraînés par l'air. On les installe en aval des refroidisseurs de sortie pour extraire l'humidité condensée. Les séparateurs d'eau ne doivent pas être confondus avec les séparateurs d'huile que l'on emploie dans les compresseurs rotatifs à vis lubrifiés pour récupérer le lubrifiant dans l'air comprimé de refoulement.
Tous les séparateurs, filtres, sécheurs et réservoirs doivent être équipés de dispositifs de purge destinés à évacuer les condensats liquides du système d'air comprimé. Des dispositifs de purge défectueux peuvent laisser s'écouler vers l'aval des bouchons d'humidité risquant de surcharger le sécheur d'air et d'obstruer les équipements finals. Des dispositifs de purge mal conçus ou médiocrement entretenus peuvent entraîner des pertes importantes d'air comprimé.
Pour une installation fonctionnant sur deux quarts de travail (4 250 heures par an), le remplacement d'un purgeur manuel qui laisse fuir en permanence 5 pcm d'air comprimé permettra d'économiser annuellement 425 $ environ.
Il existe quatre grandes méthodes de purge des condensats :
- Purgeurs automatiques à dépression avec réservoirs. C'est la méthode la plus efficace, car seuls les condensats sont évacués. Ces purgeurs sont en principe simples à tester et à entretenir. Du fait que les condensats s'écoulent normalement par gravité, la configuration de l'installation est cruciale pour éviter la formation de bouchons d'air.
- Robinets électromagnétiques à commande électrique. S'ils sont réglés pour une purge à la teneur maximale en humidité, ces types de purgeurs vont gaspiller de l'air durant les périodes de faible teneur en humidité. Le robinet électromagnétique s'ouvre pendant un temps déterminé en fonction d'un intervalle réglé à l'avance. Dans certaines circonstances, la durée pendant laquelle le robinet est ouvert est insuffisante pour vidanger de façon appropriée les condensats.
- Purgeurs mécaniques à flotteur. Ces types de purgeurs sont ordinairement difficiles à tester au niveau de leur fonctionnement et aussi à entretenir. Ils présentent souvent des points de fuite. Lorsqu'ils fonctionnent correctement, ces purgeurs ne perdent pas d'air, mais ils exigent en général beaucoup d'entretien car ils sont souvent bloqués par les sédiments.
- Purgeurs manuels. Les robinets manuels de vidange des condensats sont en principe montés dans des endroits prédisposés aux problèmes d'humidité. N'étant pas automatiques, ces robinets sont dans bien des cas laissés légèrement ouverts, ce qui occasionne des fuites d'air comprimé en permanence. Ces purgeurs sont à éviter.
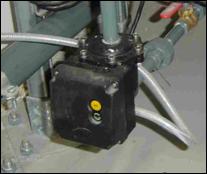
Figure 14 - Exemple de purgeur à dépression
Tuyauteries
Les tuyauteries acheminent l'air comprimé depuis la salle des compresseurs jusqu'aux appareils et procédés d'utilisation finale. La plupart des systèmes d'air comprimé font appel à des tuyauteries en acier au carbone qui sont sujettes à la corrosion. C'est pourquoi nombre de systèmes d'air comprimé doivent être équipés d'un sécheur d'air permettant de maitriser le niveau d'humidité de l'air. Un système de tuyauteries sous-dimensionnées dans la salle des compresseurs ou dans le réseau de distribution va provoquer une perte de pression notable entre le système de production d'air comprimé et les utilisations finales. Si l'on veut maintenir en aval une pression constante donnée, cette différence de pression va nécessiter une élévation de la pression de refoulement des compresseurs et, par suite, un accroissement de leur consommation d'énergie pouvant atteindre 1 % par 2 psi d'élévation de pression.
Dans la conception des tuyauteries, on devra tenir compte des aspects suivants :
- Les tuyauteries horizontales de distribution doivent comporter une légère pente vers le bas, ainsi que des dispositifs de drainage de l'humidité.
- Dans la conception d'un système d'air comprimé, une bonne pratique consiste souvent à augmenter de 30 % le débit d'air prévu (pour prendre en compte l'accroissement ultérieur éventuel du système), et à choisir un diamètre des tuyauteries entraînant la chute de pression la plus faible possible.
- Lorsque c'est possible, une bonne pratique est d'installer un réseau de distribution en boucle afin de permettre à l'air de circuler en plusieurs directions, comme le montre la Figure 17. Par rapport à une tuyauterie simple de même diamètre, une boucle de tuyauteries simples est en mesure de réduire de 75 % la différence de pression. Les boucles multiples peuvent encore améliorer l'écoulement de l'air.
Pour minimiser les pertes d'énergie dues à la différence de pression, et pour faciliter la stabilisation des pressions d'air aux extrémités de tuyauteries, le système de distribution devrait être dimensionné pour une pression différentielle ne dépassant pas 2 à 3 psi.
- Choisir, pour les tuyauteries, un matériau à faible coefficient de frottement, comme le cuivre ou l'aluminium extrudé, entraînant des pertes de pression plus faibles.
- Envisager l'emploi de tuyauteries de plus grand diamètre afin de tirer profit d'une pression différentielle plus faible.
Lorsque, pour un débit donné, on double le diamètre d'une tuyauterie, la chute de pression est en général égale à un quart de celle de la tuyauterie de diamètre simple : on économise ainsi 75 % d'énergie.
La Figure 15 montre le rapport qui existe, pour un débit d'air donné, entre la chute de pression par 1000 pieds (304 m) de longueur de tuyauterie, et différents diamètres de tuyauterie; il est à noter toutefois qu'une chute de pression supérieure à 40 psi ne peut être envisagée en pratique.
Attention : le tableau de la Figure 15 ne doit pas être employé à des fins de conception.
Pieds cubes d'air (pcnm) | Diamètre de tuyauterie, en pouces | ||||||
---|---|---|---|---|---|---|---|
1" | 2" | 3" | 4" | 6" | 8" | 10" | |
10 |
0,28 |
||||||
50 |
9,96 |
0,19 |
|||||
100 |
27,9 |
0,77 |
|||||
250 |
4,78 |
0,58 |
|||||
500 |
19,2 |
2,34 |
0,55 |
||||
750 |
43,3 |
5,23 |
1,24 |
||||
1 000 |
76,9 |
9,3 |
2,21 |
||||
2 000 |
37,4 |
8,8 |
0,99 |
||||
2 500 |
13,8 |
1,57 |
0,37 |
||||
3 000 |
20,0 |
2,26 |
0,53 |
||||
4 000 |
35,5 |
4,01 |
0,94 |
0,28 |
|||
5 000 |
55,6 |
6,3 |
1,47 |
0,44 |
Diamètre de tuyauterie (pouces) | Débit équivalent (pcnm) |
---|---|
1 | 36 |
2 | 263 |
3 | 431 |
4 | 909 |
6 | 2 679 |
8 | 6 757 |
10 | 14 286 |
Chaque chute de pression égale à 2 psi et provoquée par une tuyauterie sous-dimensionnée ou comportant des goulots d'étranglement, entraîne une augmentation approximative de 1 % de l'énergie consommée.
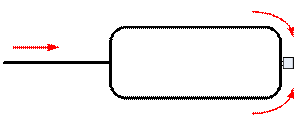
Figure 17 - Tuyauterie configurée en boucle : trajets multiples de fourniture d'air
Pour minimiser les chutes de pression, on devra lorsque la situation s'y prête, employer des raccords d'angle et raccords de jonction lisses et progressifs. Ce ne sera pas toujours possible avec des raccords filetés en fer noir, mais avec une planification soignée, le système pourrait être agencé de façon à minimiser les changements de directions.
Les raccords, coudes et points de raccordements aux tuyauteries de distribution provoquent des chutes de pression. La Figure 18 donne des indications en ce qui concerne la chute de pression approximative entraînée par certains accessoires de tuyauterie, exprimée en termes de longueur équivalente de tuyauterie rectiligne.
Attention : Le tableau de la Figure 18 est purement informatif et ne doit pas être employé à des fins de conception de systèmes de tuyauteries.
Longueur équivalente de pertes par frottement - par pied de tuyauterie rectiligne (pieds) |
||||||||
---|---|---|---|---|---|---|---|---|
Accessoire de raccordement | Diamètre nominal de la tuyauterie (pouces) | |||||||
0,50 | 0,75 | 1,00 | 1,50 | 2,00 | 3,00 | 4,00 | 6,00 | |
Coude à 90o | 1,5 | 2 | 2,5 | 4 | 5,7 | 7,9 | 12 | 18 |
Coude à 45o | 0,8 | 1,1 | 1,4 | 2,1 | 2,6 | 4 | 5,1 | 8 |
Robinet-vanne | 0,3 | 0,4 | 0,6 | 1 | 1,5 | 3 | 4,5 | 6,5 |
Té - écoulement dans le collecteur | 1 | 1,4 | 1,7 | 2,7 | 4,3 | 6,2 | 8,3 | 12,5 |
Té - écoulement dans l'embranche-ment | 4 | 5 | 6 | 8 | 12 | 16 | 22 | 32,7 |
Adaptateur mâle /femelle | 1 | 1,5 | 2 | 3,5 | 4,5 | 6,5 | 9 | 14 |
Régulateurs de débit
Ces dispositifs (parfois appelés régulateurs intermédiaires ou détendeurs) sont normalement installés près du côté refoulement de la salle des compresseurs et ont pour rôle de stabiliser la pression avec davantage de précision que les dispositifs de régulation des compresseurs. Ils peuvent être à régulation pneumatique ou être munis de dispositifs électroniques de régulation proportionnelle intégrale (PID) très précis. De tels robinets permettent d'atteindre une bien meilleure stabilité de pression dans le système ainsi qu'une meilleure efficacité due à une pression moyenne plus faible dans l'installation.
Pour les demandes d'air sans régulation, la consommation due aux fuites d'air et aux utilisations finales de l'installation sera d'autant plus élevée que le sera la pression moyenne dans le système. Ce débit supplémentaire, appelé demande artificielle, entraîne une consommation d'énergie plus élevée des compresseurs.
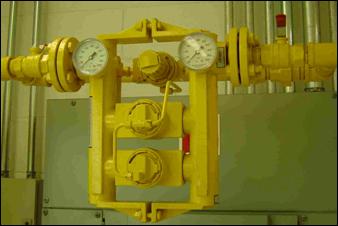
Figure 19 - Régulateur de débit
Dans les situations où une partie importante de la charge ne fait l'objet d'aucune régulation, des économies de l'ordre de 1 % pour chaque psi de pression réduit peuvent être réalisées si l'on parvient à diminuer la pression. Ces économies resteront toutefois minimales dans les cas où la majorité des utilisations finales sont bien régulées.
Dans la régulation de débit, il convient de tenir compte des aspects suivants :
- Les régulateurs de débit isolent les compresseurs des réservoirs de stockage situés en aval. Il est important de prévoir une capacité de stockage suffisante côté compresseurs du système de régulation de débit, sous peine de fréquence plus élevée des cycles des compresseurs et d'une plus grande consommation d'énergie de ceux-ci.
- En faisant fonctionner le compresseur à une pression de refoulement plus élevée que la normale du côté amont de régulation du débit, on crée une perte d'énergie. Toutefois, le fait de fonctionner avec une pression plus élevée permet d'emmagasiner davantage d'air, ce qui permet d'éviter de démarrer un compresseur supplémentaire lors des périodes de pointe et de pénaliser la demande de pointe. On devra étudier avec attention le coût en énergie qu'entraîne une telle pratique.
Groupes de détente pneumatiques
Groupe de détente pneumatique. Dans les systèmes d'air comprimé, la régulation de pression peut se situer à l'emplacement même de l'utilisation finale. Souvent, le régulateur fait partie d'un ensemble appelé groupe de détente pneumatique (GDP). Un dispositif de lubrification est parfois installé à proximité d'un point d'utilisation finale pour lubrifier des outils ou autres machines pneumatiques. On peut combiner le dispositif de lubrification à un filtre et à un régulateur de pression pour former un GDP.
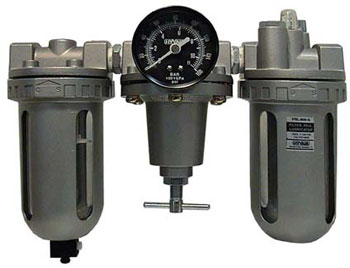
Figure 20 - Groupe de détente pneumatique (avec la permission de Hyvair)
Avec l'utilisation des GDP, il convient de tenir compte des aspects suivants :
- Le filtre choisi devra être dimensionné pour la pression différentielle minimale et le débit le plus élevé alimentant l'appareil. On consultera les courbes du fabricant qui sont fournies sur dans la plupart des fiches techniques.
- On devra employer des régulateurs de précision muni de diaphragmes de grande dimension afin de réduire la chute de pression typique qui caractérise les régulateurs peu coûteux. On consultera les courbes du fabricant pour déterminer les caractéristiques de pression des appareils.
- Les régulateurs ouverts au maximum (réglés pour suivre la pression du système) provoquent des différences de prèssion durant les débits de pointe. On devra envisager de déposer ces appareils pour obtenir de meilleures pressions aux points desservis.
- On devra maintenir remplis les dispositifs de lubrification afin qu'ils assurent une lubrification adéquate des outils raccordés au système d'air comprimé. Un outil pneumatique correctement lubrifié fonctionne mieux et consomme moins d'air comprimé.
Accessoires de raccordement
Les raccords et coupleurs pour tuyaux d'air flexible doivent être durables et étanches. Souvent, les colliers de serrage employés sur les tuyaux d'air sont achetés à bas prix et leur rendement se détériore après une certaine période de temps, comme le montre la Figure 21.
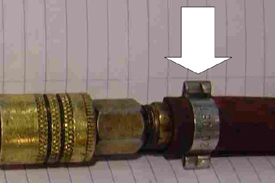
Figure 21 - Exemple de collier de serrage de tuyau flexible présentant des fuites
Les raccords rapides peuvent être une cause importante de chutes de pression. Il arrive souvent que l'air doive traverser plusieurs raccords pour alimenter l'application finale, chaque raccord provoquant jusqu'à 7 psi de baisse de pression par rapport à son débit nominal. Il n'est pas rare de constater des différences de pression allant jusqu'à 30 psi à travers tuyaux flexibles et raccords. On y remédiera en utilisant des raccords et tuyaux surdimensionnés qui donnent des différences de pression minimales.
Il est possible d'améliorer les tuyaux flexibles en employant des colliers de serrage plus solides et des raccords à connexion/déconnexion rapide étanches à l'air comme ceux illustrés dans la Figure 22.
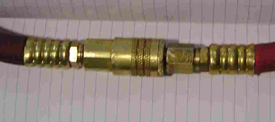
Figure 22 - Tuyau d'air flexible étanche à l'air
Usages normaux et usages abusifs de l’air comprimé
L'air comprimé est employé dans de nombreuses applications industrielles (voir Figure 23). Le coût de production de l'air comprimé est souvent inconnu de ses utilisateurs, ce qui fait que cet air est habituellement employé de façon inefficace.
Pour bon nombre d'applications, d'autres sources d'énergie peuvent s'avérer plus efficaces et moins énergivores. De façon générale, moins de 10 % de l'énergie consommée à l'origine pour la production de l'air comprimé est réellement transformée en travail utile par l'application finale. Il serait bon de recenser les équipements en service dans votre installation et de vous demander laquelle ou lesquelles de ces applications gagneraient à être transformées de façon à utiliser une autre source d'énergie.
Figure 23 - Usages courants de l'air comprimé
Agitation des liquides | Agitation des liquides | Agitation des liquides |
Freins à air comprimé | Freins à air comprimé | Freins à air comprimé |
Entraînement de pistons à air | Entraînement de pistons à air | Entraînement de pistons à air |
Mélangeage | Mélangeage | Mélangeage |
Embouteillage | Embouteillage | Embouteillage |
Serrage | Serrage | Serrage |
Nettoyage | Nettoyage | Nettoyage |
Régulations et actionneurs | Régulations et actionneurs | Régulations et actionneurs |
Transport pneumatique | Transport pneumatique | Transport pneumatique |
Usages inappropriés de l'air comprimé
Les usages inappropriés ou abusifs de l'air comprimé se définissent comme les applications qui pourraient fonctionner d'une façon plus économique et plus efficace à l'aide d'une autre source d'énergie que l'air comprimé.
Bien que constituant l'une des sources les plus coûteuses d'énergie dans une installation, l'air comprimé est d'accès facile et son adaptation à une application est simple. C'est pourquoi on l'utilise couramment dans des applications pour lesquelles d'autres technologies et sources énergétiques se révéleraient plus efficaces et plus économiques.
Des exemples d'usages inappropriés courants de l'air comprimé sont présentés dans la Figure 24.
Usage inapproprié de l'air comprimé | Description et exemple | Solutions éventuelles |
---|---|---|
Équipements abandonnés |
|
|
Aspiration |
|
|
Pulvérisation |
|
|
Transport en phase dense |
|
|
Soufflage libre |
|
|
Dispositifs de refroidissement des équipements ou du personnel |
|
|
Équipement non régulé |
|
|
Production de vide |
|
|
Ainsi, vous vous apprêtez à évaluer un système d’air comprimé ?
L'évaluation de votre système d'air comprimé est la première étape dans l'amélioration de son rendement énergétique. Les entreprises intéressées à évaluer leur système d'air comprimé peuvent le faire en faisant appel à leurs experts internes ou éventuellement à un consultant ou à un entrepreneur habilité. L'évaluation initiale consiste en une série de contrôles précis complétée par des vérifications ponctuelles continues. Il convient de procéder de façon méthodique, c'est-à-dire réaliser une analyse de chacun des composants et de la façon dont ils interagissent.
Un spécialiste qualifié peut vous aider à réaliser l'évaluation et à formuler les recommandations visant l'amélioration du système. Demandez à votre entreprise d'électricité une liste des firmes habilitées et expérimentées de votre région. Nombre de distributeurs d'électricité provinciaux et municipaux offrent des services d'assistance technique pour de telles évaluations. Vous pourriez même obtenir une aide financière auprès des gouvernements fédéral et provinciaux, et des entreprises d'électricité locales, pour couvrir une partie des coûts de l'évaluation du système et de la mise en œuvre de mesures d'amélioration des immobilisations.
Une fois que les paramètres importants du fonctionnement du système dans son ensemble ont été mesurés et que vous avez bien compris ce fonctionnement, les secteurs auxquels il faudra prêter attention seront mis en évidence.
D'autres initiatives d'amélioration devront surtout se concentrer sur les anomalies constatées durant l'évaluation initiale, en parallèle avec la surveillance continue des fuites d'air, des pressions dans le système, des débits et températures, de la qualité de l'air, de la consommation d'énergie et des points de consigne des dispositifs de régulation.
Les étapes courantes d'un programme d'amélioration d'un système d'air comprimé comprennent notamment :
- Le relevé et la collecte des caractéristiques nominales des équipements, des volumes des réservoirs, des diamètres et longueurs des tuyauteries, et l'établissement d'un schéma du système.
- L'établissement d'une base de références en mesurant les niveaux actuels de rendement du système d'air comprimé.
- L'établissement des niveaux prescrits de rendement en matière de pressions, de consommation d'énergie et de qualité de l'air du système.
- L'analyse des données de rendement, l'examen de l'historique de fonctionnement, le relevé et le calcul des coûts de fonctionnement en vue d'identifier les points qui exigent des améliorations.
- L'évaluation des variantes de configurations du système et des autres mesures d'amélioration en vue de déterminer les meilleures options techniques et économiques.
- La détermination des meilleures options techniques et économiques d'optimisation des sous-composantes du système.
- L'élaboration d'un plan de mise en œuvre des améliorations pour parvenir à une optimisation permanente.
- L'analyse des pratiques d'entretien et d'achat.
- La prise en compte des anomalies actuelles et des besoins futurs de l'installation en matière d'air comprimé.
- Une réponse à la question : existe-t-il une meilleure méthode d'approvisionnement et d'utilisation de l'air comprimé ?
Les besoins en air comprimé sont définis en termes de qualité et de quantité de l'air, et du niveau de pression recherché pour les utilisations finales dans votre installation. Une analyse approfondie des besoins va garantir qu'un système d'air comprimé possède une configuration adéquate. Le coût de production de l'air comprimé est d'autant plus élevé que l'est la qualité de l'air. Un air de qualité plus élevée nécessite en principe des équipements additionnels, ce qui non seulement augmente les investissements initiaux en capital, mais rend plus coûteux le fonctionnement de l'ensemble du système en termes de consommation d'énergie et de coûts d'entretien.
Collecte des caractéristiques nominales des équipements
Une première étape du processus consiste à collecter les caractéristiques nominales des équipements. Pour cela, on relève les données des plaques signalétiques et des rapports d'exploitation, manuels d'utilisation et bons de commande.
On devra, dans ce recensement, relever les informations et points de consigne figurant sur les plaques signalétique de tous les équipements du système d'air comprimé, y compris les compresseur(s) d'air, refroidisseurs de sortie, sécheurs d'air, réservoirs, filtres et dispositifs de régulation. Il faudra faire un schéma de votre système de production et de distribution d'air comprimé en y indiquant les dimensions des tuyauteries, les points de prise d'air, et les soupapes ou robinets. On relèvera également le type et les caractéristiques des machines ou outils situés au long du parcours du système d'air comprimé.
Établissement d'une base de références
En vue d'établir la base de références de votre système, vous devrez mesurer plusieurs paramètres de rendement. La base de références va en principe comporter un profil des charges d'air comprimé. Ce profil montre de quelle façon la demande en air et la consommation d'énergie des compresseurs varient avec le temps. Une installation présentant de courtes périodes de forte demande trouverait avantage à la mise en place d'installations de stockage, alors qu'une installation avec un profil de charges variable tirerait probablement parti de modes de régulation sophistiqués.
La Figure 25 montre un exemple de profil de charge.
L'évaluation d'un système d'air comprimé doit en principe comporter les mesures, évaluations et calculs ci-après :
- Mesures des pressions d'air en fonction du temps.
- Différences de pression en divers emplacements entre le refoulement du compresseur et les utilisations finales importantes.
- Consommation en ampères ou en kW du compresseur en fonction du temps. (Note : les mesures électriques ne doivent être effectuées que par du personnel habilité).
- Débit d'air dans le système (calculé ou mesuré directement), de préférence en fonction du temps. Ce débit se calcule facilement en utilisant la durée en charge par rapport à la durée totale de fonctionnement dans le cas de compresseurs munis d'un compteur horaire.
- Températures ambiantes et d'air des compresseurs.
- Coûts d'exploitation calculés pour l'électricité, (eau ou eau réfrigérée), l'entretien et les taxes à partir des données recueillies.
- Identification et mesure des fuites dans le système.
- Chutes de pression ou pressions différentielles aux équipements desservis.
- Identification des usages abusifs de l'air comprimé.
- Évaluation des dispositifs de filtration d'air en termes de chutes de pression et d'efficacité.
- Évaluation des réservoirs d'air comprimé.
- Évaluation des sécheurs d'air (points de rosée prescrits, consommation d'énergie et chutes de pression spécifiés).
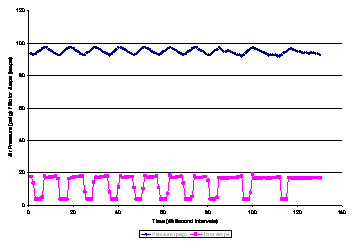
Figure 25 - Exemple de profil de la pression d'air comprimé et du courant absorbé par le moteur (avec la permission de Manitoba Hydro)
Analyse des données de rendement et fixation des niveaux de rendement
Une fois les mesures effectuées et les normes de rendement fixées, on peut procéder à l'analyse des données en vue de déterminer si le système répond aux besoins de l'installation. L'analyse devra faire ressortir les domaines d'anomalies et identifier les possibilités d'amélioration éventuelles.
L'optimisation du rendement maximal d'un compresseur d'air nécessite une étude de la relation et de l'interaction des composantes qui constituent le système, en plus d'une évaluation distincte de chaque composante.
Les aspects à évaluer comprennent :
- Type, puissance et état des compresseurs. On évaluera les compresseurs pour déterminer s'ils conviennent à l'usage prévu et pour connaître leur état général. On peut estimer l'efficacité d'un compresseur à partir des spécifications du fabricant adaptées aux conditions du site. L'installation d'un compresseur doit également être évaluée en termes d'emplacement, d'admission d'air, de ventilation et de récupération de chaleur.
- Réservoirs primaires et secondaire. On évaluera l'efficacité du réservoir d'air comprimé en termes d'emplacement et de dimension. Dans l'ensemble, les compresseurs d'air doivent montrer qu'ils sont en mesure de satisfaire les besoins en air du système - sauf pour de courtes périodes de temps de demande élevée pendant lesquelles l'air pourra être fourni par un ou plusieurs réservoirs. On devra également penser à répondre à d'éventuelles demandes à l'aide de réservoirs d'air secondaires.
- Dispositifs de régulation des compresseurs. Vérifier que les points de consigne sont appropriés. Dans le cas de compresseurs multiples, les plages de pression de mise en marche ou à l'arrêt d'un compresseur doivent être réglées.
- On examinera la propreté des filtres de même que leur adéquation à l'application. Les chutes de pression à travers les filtres devront être évaluées aux fins d'estimation des pertes d'énergie entraînées par le filtre considéré. On vérifiera que le programme d'entretien et de changement des filtres est approprié, et l'on envisagera l'achat de filtres plus efficaces.
- On peut mesurer le rendement des refroidisseurs de sortie et séparateurs d'humidité, ainsi que l'efficacité du refroidissement; on recommandera alors des modifications réalisables ou l'installation de nouveaux systèmes.
- On vérifiera si les sécheurs d'air conviennent aux usages prévus de l'air comprimé rencontrés dans l'installation. Il est important de consigner la taille des sécheurs, les chutes de pression, le rendement global des sécheurs, et d'envisager des modifications à ces derniers en fonction des spécifications de volume et de qualité de l'air.
- Purgeurs automatiques. L'emplacement, l'état et l'efficacité de tous les purgeurs devront être évalués; des options visant une meilleure efficacité énergétique devront être recommandées s'il y a lieu.
D'autres aspects à prendre en compte incluent :
- Stabilité de la pression du système (l'usine présente-t-elle des problèmes de pression).
- Puissance spécifique du système (combien faut-il de kW pour produire 100 pcm) ou combien de $ par 100 pcm.
- Stabilité des points de rosée (présence d'eau dans l'air).
- Débits de pointe, débit moyen et débit minimal (le système de production est-il en mesure d'assurer ces débits de façon appropriée).
- Températures de crête, moyenne et minimale de la salle des compresseurs (les compresseurs et sécheurs sont-ils en mesure de fonctionner correctement dans ces conditions).
- Coûts annuels et horaires d'entretien et de fonctionnement (est-il plus coûteux d'entretenir un compresseur que d'en acheter un nouveau).
Mise sur pied d'un plan
Une fois que les débits de pointe et moyen sont connus et que les niveaux de rendement ont été établis, il devient possible de calculer la valeur des économies d'énergie en fonction des différentes solutions.
Les éléments à prendre en compte comprennent :
- Identification des équipements qui peuvent être arrêtés.
- Choix et utilisation des dispositifs de régulation des compresseurs et des régulateurs de débit.
- Possibilités de réduction de la taille des équipements ou d'achat de nouveaux équipements s'il y lieu.
- Évaluation des possibilités de minimiser les heures de fonctionnement des équipements d'air comprimé.
- Choix approprié des compresseurs d'air (nombre d'étages, type de compresseur et modes de régulation).
Au moment du choix d'équipements neufs ou de remplacement destinés à votre système d'air comprimé, rappelez-vous d'appuyer votre décision sur le coût global de fonctionnement du cycle de vie prévu. Évitez les décisions d'achat ne reposant que sur le prix initial. Procurez-vous les spécifications techniques des compresseurs auprès du Compressed Air Gas Institute (CAGI) afin de comparer les caractéristiques à pleine charge d'une marque par rapport à une autre. En plus de vous donner un avis impartial, votre entreprise d'électricité locale vous proposera souvent les noms de spécialistes qualifiés, dans votre région, en mesure de vous aider dans la planification de votre système d'air comprimé.
Points à prendre en compte pour engager un vérificateur en air comprimé
Vous aurez parfois besoin d'aide pour entreprendre une évaluation en matière d'air comprimé ou pour planifier l'expansion d'un nouveau système. Voici une liste de questions méritant réflexion et qui pourraient vous aider à prendre votre décision¹:
- Quelles sont les références antérieures et quel est le niveau de connaissance de l'entreprise et de la personne qui vont procéder au travail ?
- Dans quelle mesure le fournisseur de services comprend-il bien les notions d'efficacité énergétiques et de compromis en matière d'économie ?
- À quel point le fournisseur de services est-il familier avec la totalité des aspects et des types de compresseurs d'air, y compris l'alimentation en air et la demande d'air ?
- Dans quelle mesure connaît-il bien les autres équipements et dispositifs connexes ? (sécheurs, filtres, réservoirs, tuyauterie, applications, etc.)
- Dans quelle mesure le fournisseur de services comprend-il bien mon industrie et les produits que nous fabriquons ou que nous transformons ?
- Jusqu'à quel point son rapport ou ses conseils seront-ils objectifs ? (Tente-il juste de nous vendre des équipements ou des services supplémentaires, ou bien son travail a-t-il été effectué de manière impartiale et indépendante?)
- À quel point le fournisseur de services est-il réceptif ? (se montre-t-il disponible pour faire des essais en minimisant les impacts sur l'installation et/ou pour procéder à ces essais pendant les nuits/fins de semaine)
- Les essais pourront-ils être effectués avec un minimum de supervision ?
- Que comprendra l'évaluation du système d'air comprimé et quel sera le type de rapport final fourni ?
- Le rapport final pourra-t-il être présenté à la direction aux fins d'élaboration d'un programme de rendement énergétique et d'une analyse de rentabilisation ?
- À quel point le fournisseur de services est-il réceptif en ce qui a trait aux pratiques et procédures de santé et sécurité ?
Mesures d’efficacité énergétique éprouvées
Cette section décrit les mesures éprouvées depuis longtemps en matière d'amélioration de l'efficacité énergétique des systèmes d'air comprimé et notamment :
- Identification et réparation des fuites d'air,
- Minimisation des chutes de pression,
- Minimisation de l'utilisation finale d'air comprimé,
- Faisabilité de récupération de chaleur des compresseurs,
- Optimisation des équipements de production d'air,
- Optimisation des équipements de production d'air.
Fuites d'air dans les systèmes d'air comprimé
Les fuites d'air peuvent constituer une part importante de l'énergie gaspillée dans un système d'air comprimé et se traduire, dans certaines circonstances, par des pertes de productivité. Dans des installations industrielles types, il n'est pas rare de déceler des fuites d'air représentant entre 20 et 30 pour cent du débit d'un compresseur. Des programmes proactifs de gestion des fuites (détection et réparation) peuvent réduire les fuites à moins de 10 pour cent de la production d'air comprimé d'une usine.
L'expérience a montré maintes fois que la réparation des fuites d'air constituait le plus souvent la priorité essentielle dans l'optimisation de tout système d'air comprimé. En général, vous pourrez constater que vos initiatives verront une période de récupération simple inférieure à 6 mois.
En plus d'être une source de gaspillage d'énergie, les fuites d'air peuvent contribuer à d'autres pertes d'exploitation. Il existe une relation marquée de cause à effet entre le nombre et l'ampleur des fuites d'air et la pression dans l'ensemble du système d'air comprimé. Par exemple, une pression d'air comprimé plus faible va nuire à l'efficacité des outils et équipements pneumatiques en diminuant leur puissance mécanique et en abaissant ainsi la productivité d'un procédé.
Un manqué d'intérêt envers la gestion des fuites d'air peut conduire à l'achat inutile de nouveaux compresseurs d'air, augmentant par là les dépenses d'investissement.
La Figure 26 présente le coût annuel approximatif en électricité (0,10 $/kWh) pour différentes quantités de fuites en se basant sur une exploitation à un, deux ou trois quarts de travail.
Le type de régulation des compresseurs peut avoir un effet marqué sur les résultats d'une initiative de réduction des fuites. Par exemple, une initiative de réduction des fuites visant à diminuer de 10 % la consommation d'air dans un système avec un seul compresseur à régulation par modulation, aboutira à des économies d'énergie de seulement 3 % environ du fait de la marge de réglage effective limitée de la régulation par modulation du compresseur. Une même initiative de réduction appliquée à un système avec compresseur à vitesse variable entraînerait des économies d'énergie de l'ordre de 10 %.
Quantités de fuites | 1 quart de travail (2 250 h) | 2 quarts de travail (4 250 h) | 3 quarts de travail(8 400 h) |
---|---|---|---|
Fuite de 1/16 po | 200 $ | 380 $ | 750 $ |
Fuite de ¼ po | 3 210 $ | 6 070 $ | 11 990 $ |
Fuite de 3/8 po | 7 230 $ | 13 650 $ | 26 980 $ |
Fuite de ½ po | 12 820 $ | 24 210 $ | 47 850 $ |
Estimation des fuites d'air totales
Pour aborder le problème des fuites d'air dans une usine, une première étape souhaitable consiste à effectuer un essai à faible charge pendant un arrêt de production. Cet essai peut s'avérer assez facile s'il existe déjà un débitmètre de précision installé sur le système ou si les compresseurs d'air sont équipés de d'indicateurs de débit. Si ce n'est pas le cas, on pourra effectuer un essai spécial en employant un ou plusieurs des compresseurs d'air de l'usine.
Si les compresseurs de l'usine fonctionnent déjà en mode en charge/à vide (un fournisseur de services en compresseurs peut aider à le déterminer), une estimation des fuites peut être réalisée en mesurant les durées en charge et à vide pendant lesquelles le compresseur alimente les fuites. Par exemple, si un compresseur de 100 HP a un débit nominal de 400 pcm et fonctionne en charge pendant 2 minutes et à vide pendant 3 minutes, on estime la charge de fuites en prenant le temps en charge et en le divisant par le temps total de fonctionnement en charge et à vide, soit dans cet exemple 2/5 = 0,4. Ceci signifie que le compresseur fonctionne en charge pendant 40 % du temps. La charge de fuites sera alors de 40 % de 400 pcm soit 160 pcm. Si un autre compresseur fonctionnait en charge pendant ce temps, sa capacité devrait être ajoutée à cette valeur calculée. En général, la capacité de sortie d'un compresseur fonctionnant aux environs de 100 psi sera près de 4 fois la puissance nominale en HP figurant sur sa plaque signalétique.
On peut aussi réaliser cet essai avec des compresseurs régulés par modulation à l'aide d'un indicateur de pression de précision et d'un chronomètre. Comme cet essai provoque d'importantes variations de pression, il est important de déterminer si des équipements critiques vont être affectés.
Si l'usine peut tourner avec un seul compresseur en marche, on réalisera l'essai de fuites en arrêtant le compresseur et en mesurant le temps nécessaire pour que la pression tombe d'une valeur de 10 psi inférieure à la pression normale du système jusqu'à une valeur de 30 psi plus basse (chute de 20 psi). Cet essai est effectué à une faible valeur afin d'éviter une modulation du compresseur au cours l'expérience.
Pour la deuxième partie de l'essai, on remet le compresseur en marche, puis on mesure les durées nécessaires pour que la pression s'élève et atteigne ces deux mêmes valeurs. On répète l'essai à plusieurs reprises en prenant garde de ne pas dépasser 4 démarrages de moteur par heure. Le facteur de charge du compresseur est déterminé en prenant le temps d'élévation de pression et en le divisant par le temps total (chute plus élévation de pression). Comme dans l'exemple qui précède, la charge de fuites est estimée en multipliant ce facteur par le débit de refoulement du compresseur en pcm. Au cas où un second compresseur a été nécessaire pour atteindre la pression voulue, son débit devra être ajouté au total.
Le coût approximatif d'alimentation de ces fuites sous 100 psi peut être déterminé comme suit :
0,2 × pcm de fuite × heures par an × coût du kWh
Le fait de négliger un débit de fuite de 100 pcm coûtera donc environ 0,2 × 100 × 4 250 × 0,10 $ = 8 500 $ par an, pour un tarif moyen de l'électricité de 10 cents le kWh.
Comment repérer les fuites d'air
Les fuites d'air sont très difficiles à voir ou à entendre dans des environnements comportant un bruit de fond important (par ex. ventilateurs ou machines).
Le meilleur moment pour découvrir les fuites d'air est celui des périodes d'arrêt de l'usine, habituellement pendant la nuit ou durant les fins de semaine. Marchez le long du système de distribution d'air comprimé ou sur son périmètre. Arrêtez-vous de temps à autre et tentez d'écouter les fuites. Recherchez les raccords endommagés ou les tuyaux flexibles fissurés. Prenez des notes et faites un croquis de l'emplacement des fuites. Employez des étiquettes pour repérer les emplacements des fuites à réparer. Répétez le processus périodiquement dans le cadre de votre inspection de routine.
Lorsque l'usine est à l'arrêt, on peut souvent entendre les fuites d'air. S'il existe un bruit de fond, vous devrez probablement vous servir d'un détecteur de fuites à ultrasons. Les détecteurs de fuites à ultrasons sont des appareils portatifs qui détectent la présence de fuites d'air grâce à leurs caractéristiques ultrasoniques. Après avoir détecté l'emplacement d'une fuite d'air, on doit appliquer de l'eau savonneuse sur les endroits suspects. La méthode de l'eau savonneuse est très fiable, mais elle exige beaucoup de temps à mettre en œuvre.
Attention : Utilisez toujours des équipements de protection de l'ouïe et de la vue appropriés et respectez les procédures de sécurité adéquates pour la détection des fuites d'air ou le travail en hauteur.
L'expérience a montré que les fuites d'air se produisent le plus souvent aux joints et aux raccordements. La réparation d'une fuite peut consister à simplement resserrer un collier de serrage ou à remplacer l'équipement défectueux tel que :
- Coupleurs
- Raccords
- Sections de tuyauteries
- Tuyaux flexibles
- Joints
- Drains à siphon
- Embouts servant à minimiser les fuites d'air
- Tiges de soupape
Prévention des fuites
Voici quelques conseils facilitant dès le départ la prévention des fuites :
- Installez les raccords correctement en employant, s'il y a lieu, les produits d'étanchéité voulus.
- Isolez du système de distribution, au moyen d'un robinet, les équipements non utilisés.
- Lorsque c'est possible, diminuez la pression d'air dans le système. Une plus basse pression différentielle à l'endroit d'une fuite d'air réduit légèrement le débit de fuite, mais ce n'est pas là un remède pour réparer les fuites d'air.
- Choisissez des accessoires (tuyaux d'air flexibles, tubulures, raccords rapides) de première qualité provenant de fournisseurs reconnus.
Rappelez-vous qu'après réparation des fuites, si l'on souhaite tirer pleinement parti des économies d'énergie, il est souvent nécessaire de rajuster les régulateurs du compresseur.
Diminution de la pression de refoulement du compresseur en minimisant les chutes de pression
La pression de refoulement d'un compresseur influe sur son rendement. Dans de rares occasions, il arrive que la pression de refoulement d'un compresseur a été involontairement réglée à une valeur trop élevée sans raison valable. Un simple réglage des points de consigne du compresseur à des valeurs moins élevées va alors permettre de réaliser des économies d'énergie. On devra dans ce cas procéder avec précaution et par petites étapes, de façon à ne pas nuire aux équipements sensibles de l'installation ou de l'usine.
Toutefois, la plupart du temps, la pression de refoulement d'un compresseur est réglée arbitrairement à un niveau élevé afin de compenser les diverses chutes de pression se manifestant dans le système entre le compresseur et les utilisations finales cruciales. Les chutes de pression sont provoquées par les résistances à l'écoulement à l'intérieur du système de tuyauteries et des ses composantes. Une chute de pression trop radicale peut se traduire par un mauvais rendement du système et une consommation d'énergie excessive du compresseur.
Les coûts monétaires et en électricité de la production d'air comprimés sont directement liés à la pression de refoulement du compresseur. La pression de refoulement d'un compresseur est bien souvent réglée à des valeurs de pression plus élevées que celles normalement nécessaires. Voici une règle empirique pour les systèmes fonctionnant dans la gamme des 100 psi : pour chaque accroissement de 2 psi de la pression de refoulement, il faut compter une augmentation approximative de 1 % de la consommation d'énergie au plein débit de sortie. Ce chapitre traite de la question des chutes de pression et explique comment vous pouvez les éliminer ou les minimiser.
Les endroits les plus critiques des chutes de pression sont : refroidisseurs de sortie, filtres, séparateurs d'eau, sécheurs d'air, tuyauteries et clapets antiretour. Tout endroit opposant une résistance à l'écoulement à l'intérieur d'un système d'air comprimé nécessite des pressions de service plus élevées et, par conséquent, une consommation plus importante d'énergie.
En général, un système d'air comprimé convenablement conçu devrait présenter une perte (ou chute) de pression bien inférieure à 10 pour cent de la pression de refoulement du compresseur, cette perte étant mesurée entre le point de refoulement et celui d'utilisation finale.
Méthodes pour minimiser les chutes de pression
La liste qui suit propose quelques méthodes courantes visant à minimiser les chutes de pression dans un système d'air comprimé :
Il est recommandé de choisir les composants des appareils de traitement d'air tels que refroidisseurs de sortie, séparateurs d'humidité, sécheurs d'air et filtres, présentant la chute de pression pratique la plus faible possible dans les conditions de fonctionnement maximales précisées. Une fois les composants installés, on devra respecter et documenter les procédures d'entretien recommandées du fabricant. Voici d'autres conseils pour la gestion des chutes de pression :
- Entretenir les appareils de filtration et de séchage d'air afin d'amenuiser les effets de l'humidité, comme par exemple la corrosion des tuyauteries.
- Concevoir correctement le système de distribution en prévoyant des tuyauteries de diamètre approprié et des configurations en boucle lorsque c'est possible.
- Réduire la longueur des parcours de l'air à travers le système de distribution.
Dans les cas où l'on peut réduire la pression de refoulement du compresseur, on réalisera des économies d'énergie. Avant de diminuer la pression de refoulement d'un compresseur, il est important de vérifier les spécifications des équipements desservis afin de déterminer quelle est la pression minimale nécessaire au bon fonctionnement des outils et autres appareils à air comprimé.
- Évaluer les niveaux de pression exigés par les diverses utilisations finales. Minimiser la pression du système d'air comprimé pour l'adapter aux spécifications des utilisations finales.
- Vérifier si la pression de l'air à l'entrée des outils pneumatiques est suffisante. Il n'est pas rare de mesurer des chutes de pression de l'ordre de 30 à 40 psi entre l'embranchement sur le collecteur de distribution et le point d'utilisation. Cette chute de pression est souvent provoquée par des canalisations sous-dimensionnées ou à des raccords à connexion rapide, des filtres, des régulateurs et des dispositifs de lubrification. Des chutes de pression notables sont également courantes dans les tuyaux souples des utilisations finales. Il arrive régulièrement que l'appareil desservi soit alimenté par un long tuyau souple rétractable ou par une série de tuyaux souples. La différence élevée de pression qui en résulte va avoir des effets négatifs sur la puissance transformable en travail utile et va imposer souvent une augmentation des pressions dans le système principal.
- Étudier chaque point d'utilisation et déterminer celui qui nécessite la pression la plus élevée. Réduire cette pression à la valeur nécessaire au maintien de la fonctionnalité, puis diminuer ensuite la pression générale du système.
- Spécifier des régulateurs de pression, dispositifs de graissage, tuyaux souples et accessoires de raccordement présentant la pression différentielle la plus faible possible et les meilleures caractéristiques de rendement. Dimensionner les composantes pour les débits réels et non pour les débits moyens.
La pression différentielle des outils alimentés peut être facilement vérifiée en installant simplement un manomètre d'essai que l'on insère à l'aide de raccords rapides dans l'alimentation d'air à proximité de l'utilisation finale. La comparaison de la pression d'air avec ou sans consommation d'air de l'utilisation finale indiquera la pression différentielle.
- Pour réduire les pressions différentielles, employer des coupleurs de plus grande dimension. Par exemple, pour un même débit, un raccord à connexion rapide de 3/8 de pouce a une pression différentielle six fois moindre qu'un raccord de 1/4 de pouce.
Minimisation des besoins énergétiques des points d'utilisation de l'air comprimé
Voici quelques conseils qui vous aideront à minimiser les besoins énergétiques globaux de votre système d'air comprimé.
- Remplacer les applications finales inadéquates telles que soufflage libre par des modèles plus performants (buses tourbillonnaires, pulvérisateurs).
- Installer un contrôleur de débit pour réduire la pression d'air dans l'usine et diminuer la demande artificielle qu'entraînent des pressions plus élevées que nécessaire.
- Arrêter les équipements consommateurs d'air au moyen de robinets électromagnétiques ou de robinets d'arrêt manuels.
- Éviter de faire fonctionner des outils pneumatiques à vide, car leur consommation d'air est alors plus élevée qu'en charge.
- Remplacer les outils en mauvais état, car ils exigent fréquemment une pression plus élevée et consomment davantage d'air comprimé que des outils en bon état.
- Lubrifier les outils pneumatiques selon les recommandations du fabricant. Maintenir l'air employé par toutes les utilisations finales exempt de condensats afin d'optimiser la durée de vie et le rendement de ces outils.
- Lorsque cela est possible et réalisable, maintenir groupés les équipements d'utilisation finale de l'air ayant des besoins d'air comprimé semblables en termes de pression et de qualité de l'air.
Récupération de la chaleur des compresseurs
Environ 80 pour cent de l'énergie électrique consommée par un compresseur d'air industriel est transformée en chaleur. Dans bon nombre d'installations, un dispositif de récupération de la chaleur correctement conçu parvient à récupérer entre 50 et 90 pour cent de cette énergie thermique pour chauffer des locaux et de l'eau. Pour les systèmes d'air comprimé nouveaux ou en cours d'expansion, les possibilités de récupération de chaleur vont influer sur l'emplacement final du compresseur d'air à l'intérieur de l'installation.
Chauffage de l'air
Les compresseurs rotatifs à vis monoblocs constituent des candidats idéals pour la récupération de chaleur aux fins de chauffage des locaux. En général, l'air ambiant est réchauffé lorsqu'il traverse le refroidisseur de sortie et le refroidisseur d'huile du compresseur. Vu que les compresseurs monoblocs sont sous armoire et en général déjà équipés d'échangeurs de chaleur et de ventilateurs, il ne reste qu'à installer des gaines et des ventilateurs CVCA pour extraire la chaleur. Les gaines peuvent inclure un évent commandé par thermostat. L'évent peut envoyer directement l'air réchauffé vers l'extérieur lors des périodes plus chaudes de l'année. En termes d'efficacité énergétique, il est possible d'extraire environ 50 000 Btu de chaleur par heure pour chaque 100 pcnm d'air d'un compresseur fonctionnant à pleine charge.
Il n'est pas rare de pouvoir réchauffer l'air de 15 à 25 °C au-dessus de la température d'entrée de l'air de refroidissement avec un rendement de récupération de chaleur de l'ordre de 80 à 90 pour cent. Il est important de bien comprendre que pour utiliser cette chaleur récupérée, aucun conduit de ventilation de récupération de chaleur ne doit limiter le débit d'air de refroidissement du compresseur. Au cas où un grand système de gaines est installé, on devra utiliser des ventilateurs d'appoint.
Chauffage de l'eau
À l'aide d'un échangeur de chaleur approprié, il est possible d'extraire la chaleur perdue des refroidisseurs d'huile des compresseurs à pistons ou des compresseurs rotatifs à vis à refroidissement par eau du type monobloc. Certains fabricants proposent ces dispositifs en option. Cette chaleur récupérée peut servir à produire de l'eau chaude exploitable dans divers procédés : chauffage central ou systèmes de chaudières, procédés de nettoyage industriel, opérations de placage, pompes à chaleur, buanderies, ou toute autre application nécessitant de l'eau chaude. Les échangeurs de chaleur permettent également de produire à la fois de l'air chaud et de l'eau chaude, et procurent à l'exploitant la possibilité de faire varier dans une certaine mesure le rapport air chaud/eau chaude. La plupart des compresseurs à refroidissement par eau étant de puissance élevée (> 100 HP), la récupération de chaleur pour le chauffage des locaux peut constituer une option intéressante.
En principe, 50 à 60 pour cent de la chaleur des compresseurs peut être pratiquement récupérée pour des applications de chauffage de l'eau. Il est important de bien comprendre que pour utiliser cette chaleur, aucune stratégie de récupération de la chaleur ne doit limiter le débit d'eau de refroidissement du compresseur, sous peine d'entraîner une surchauffe de celui-ci.
Mise en œuvre d'un système plus efficace de régulation des compresseurs
L'analyse décrite dans la section intitulée "Dispositifs de régulation des compresseurs et rendement des systèmes" à la page 3 a montré qu'il est possible de réaliser d'importantes économies d'énergie en faisant fonctionner les compresseurs selon des modes de régulation plus performants. On ne devra tenir compte de ces considérations que pour les systèmes dont les compresseurs existants sont aptes à de tels modes de fonctionnement. Les fournisseurs locaux de services en compresseurs peuvent vous aider à améliorer ou à modifier les dispositifs déjà en place de régulation pour un fonctionnement plus efficace.
En matière de régulation des compresseurs, on devra tenir compte des aspects supplémentaires suivants :
- Pour un rendement énergétique et opérationnel optimal, les systèmes à compresseurs multiples doivent faire appel à des dispositifs ou modes de régulation plus sophistiqués (plages de pression en cascade, régulation supérieure du réseau ou du système) afin de coordonner le fonctionnement des compresseurs et la fourniture de l'air comprimé au système.
- Il est essentiel de tenir compte du facteur temps dans la conception ou le réglage du système de régulation d'un compresseur. Les compresseurs prennent un certain temps pour démarrer et atteindre leur vitesse nominale, et cela pourrait exiger une capacité de stockage supplémentaire.
- Les bandes individuelles des plages de pression en cascade doivent être ajustées de temps à autre.
- Le compresseur "d'appoint" (unité de compensation) devrait être celui qui est le plus apte à fonctionner avec un bon rendement pour des charges partielles.
Installation d'une capacité de stockage
Les réservoirs peuvent contribuer à un fonctionnement plus efficace des systèmes d'air comprimé et faciliter la stabilisation des pressions dans le système, comme on l'a exposé au paragraphe "Réservoirs et stockage de l'air comprimé" à la page 2.
On devra également tenir compte des aspects suivants :
- Lorsque cela est réalisable, installer les réservoirs aussi près que possible des compresseurs.
- Pour la plupart des installations comportant des compresseurs rotatifs à vis à régulation de type en charge/à vide, installer des réservoirs d'air d'une capacité de 10 gallons US par pcm de capacité de compresseurs.
- Lorsque des réservoirs sont exposés à des températures inférieures au point de congélation, des précautions devront être prises pour éviter le gel dans les purgeurs de condensats. Dans certains cas, on devra installer des réservoirs prévus pour des températures plus basses.
- Choisir un réservoir de capacité légèrement supérieure à ce qui serait normalement nécessaire. Cela ne fera qu'améliorer la stabilité des pressions du système et assurera une meilleure réponse aux demandes intermittentes.
- Dans le cas où l'air doit être séché, il est parfois avantageux d'installer deux réservoirs, dont l'un en amont et l'autre en aval du séchage.
Optimisation des sécheurs d'air
Les sécheurs d'air peuvent consommer des quantités considérables d'air comprimé ou d'énergie électrique; ils présentent souvent des possibilités de marge de réglage effective limitées comme on l'a exposé au paragraphe " Sécheurs d'air " à la page 3. En améliorant le sécheur d'air déjà en place ou en le remplaçant, il est possible d'obtenir de bons résultats au niveau économique. En ce qui concerne les sécheurs, tenir compte des aspects suivants :
- À l'achat de nouveaux sécheurs d'air à réfrigération, toujours prendre en compte le mode de régulation cyclique pour de meilleures économies d'énergie.
- Éviter de sécher l'air jusqu'à une valeur du point de rosée inférieure à celle qui est nécessaire pour une application donnée.
- Pour tous les types de sécheurs à régénération avec matériau déshydratant, employer des contrôleurs de point de rosée à économie d'énergie.
Réduction des purges du systèmes
Les purgeurs de condensats sont des endroits où l'on rencontre souvent des pertes d'air comprimé. Envisager de remplacer les purgeurs programmés ou les purgeurs manuels gardés entrouverts par des purgeurs à dépression. Tenir compte des aspects suivants :
- Lorsque c'est possible, acheter des purgeurs de condensats munis d'un indicateur à niveau visible, qui fournira une indication visuelle en cas de mauvais fonctionnement du purgeur.
- Tester régulièrement les purgeurs automatiques pour vérifier leur bon fonctionnement.
- Les tuyauteries doivent comporter une légère pente descendante à partir des compresseurs.
- Installer les purgeurs au bas des collecteurs principaux afin de permettre aux condensats de s'accumuler et de s'écouler par gravité.
- Éviter d'employer des robinets de purge manuels.
Achat d'un compresseur plus performant
Une bonne stratégie de gestion de l'énergie peut consister à acheter un nouveau compresseur plus performant en remplacement d'un ancien équipement. L'ancien compresseur peut souvent être conservé en réserve, procurant ainsi une capacité de secours qui améliore la fiabilité du système. Pour l'achat d'un compresseur, tenir compte des aspects suivants :
- Acheter les compresseurs offrant le rendement énergétique le plus élevé, notamment ceux équipés de moteurs à haut rendement certifiés Premium.
- Dans les installations comprenant des compresseurs multiples, faire fonctionner les groupes alimentant les charges de base à leur capacité maximale plutôt qu'à charge partielle.
- Envisager d'acheter et de faire marcher au moins un compresseur à vitesse variable assurant la fourniture d'air correspondant aux variations de débit dépassant la charge de base.
- L'achat d'un compresseur à deux étages pourra améliorer le rendement du système s'il est utilisé comme compresseur de base.
Entretien de votre système d’air comprimé
Il est important d'entretenir tous les équipements du système d'air comprimé en respectant les spécifications des fabricants. Ceci vaut plus particulièrement pour les inspections, essais, opérations d'entretien et calendriers de service recommandés qui sont spécifiés dans les manuels d'utilisation.
- Les fuites d'air nuisent aux compresseurs car elles entraînent une augmentation des coûts d'exploitation et entravent le rendement des systèmes de régulation.
- Des filtres colmatés risquent de provoquer des problèmes d'humidité lesquels vont alors exiger une purge continue et des débits d'air plus élevés.
- La pression différentielle des séparateurs d'huile fait augmenter la consommation d'énergie.
Du point de vue efficacité énergétique, il est sage dans la plupart des cas de procéder à l'entretien des équipements plus fréquemment qu'aux intervalles recommandés. Ceci est d'autant plus vrai pour ce qui touche les fuites d'air, les pressions trop élevées, l'humidité et les dispositifs de régulation.
La Figure 27 présente une liste de quelques conseils d'entretien recommandés (pour les compresseurs rotatifs à vis).
Rappelez-vous cependant que les points apparaissant dans la liste de la Figure 27 ne remplacent pas ceux cités dans les manuels des fabricants.
Fréquence ou heures de fonctionnement | Action |
---|---|
Chaque jour |
|
Chaque semaine |
|
Toutes les 3 000 heures |
|
Toutes les 15 000 heures |
|
Exemples de cas “avant et après”
Voici quelques exemples réels de décisions intelligentes visant une meilleure efficacité énergétique de systèmes d'air comprimé. Les exemples comprennent :
- Une réduction spectaculaire de la consommation d'air de purge du matériau déshydratant d'un sécheur à régénération
- L'utilisation d'un compresseur de très petite puissance pour alimenter en air des instruments pendant les fins de semaine
- Les spécifications d'une régulation tout ou rien pour un compresseur rotatif à vis.
"Avant" correspond à l'équipement déjà en place, à la méthode d'exploitation courante ou à la décision d'achat normale.
"Après" correspond à l'équipement à haut rendement énergétique choisi, à la méthode d'exploitation privilégiée ou la décision d'achat recommandée.
Cas 1 : installation d'un régulateur de purge, réparation des fuites et baisse de la pression
Une moyenne entreprise de fabrication de meubles possède deux compresseurs à vis de 100 HP exploités en mode de modulation et alimentant un sécheur d'air de 1 000 pcm fonctionnant sans régulation du débit. Le système fonctionne 6 000 heures par an et il est complètement arrêté les fins de semaine. Des problèmes de pression étant survenus à un point d'utilisation finale, il a fallu augmenter la pression de refoulement du compresseur. Le personnel de l'usine a tenté d'arrêter l'un des compresseurs pour économiser de l'énergie; mais cela a provoqué une baisse de pression au moment des débits de pointe dans l'usine pendant le quart de travail de jour, c'est-à-dire au moment où la production est à son maximum. Un audit des installations a été effectué et les données suivantes ont été recueillies :
Avant
- Production totale d'air comprimé : 450 pcm
- Consommation totale d'énergie des compresseurs : 880 000 kWh
- Puissance spécifique du système : 32,9 kW/100 pcm
- Coût total de l'électricité au prix de 10 cents/kWh : 88 000 $
- Purge du sécheur d'air : 150 pcm
- Fuites : 100 pcm
- Purgeurs : 5 pcm
- Pression de refoulement moyenne des compresseurs : 120 psi
- Pression différentielle dans le sécheur et le filtre : 10 psi
- Pression différentielle dans les tuyauteries desservant les points d'utilisation : 20 psi.
- Pression nécessaire au point d'utilisation : 80 psi
Après
Le rapport d'audit a formulé les recommandations suivantes qui ont été mises en œuvre par le client :
- Réduction des fuites : jusqu'à 50 pcm
- Réduction des purges : 5 pcm
- Réduction de la pression de l'usine de 15 psi pour une réduction de débit de 10 % : 25 pcm
- Installation d'un régulateur de purge sur le sécheur entraînant une réduction des purges de : 117 pcm
- Réduction totale du débit : 197 pcm
- La charge moyenne finale des compresseurs a été ainsi ramenée à 253 pcm
- Un des compresseurs peut maintenant être arrêté et le compresseur d'appoint va consommer 76 kW × 6000 h = 456 000 kWh ce qui représente une économie de 48 %
- Économies avec le mode actuel de régulation par modulation des compresseurs : 42 400 $ annuellement.
Autres mesures recommandées :
- Réduire de 13 psi la pression différentielle dans les tuyauteries desservant les points d'utilisation
- Réduire de 7 psi la pression différentielle dans le sécheur et le filtre
- Réduire de 20 psi de la pression de refoulement du compresseur
- Installer un compresseur à vitesse variable (VSD). Puissance moyenne de ce compresseur à 253 pcm à 100 psi : 50 kW.
Ces mesures ont procuré les économies suivantes :
- Nouvelle consommation en électricité du système : 300 000 kWh
- Nouvelle consommation spécifique du système : 19,8 kW/100 pcm
- Nouveau coût en électricité du système : 30 000 $ par an
- Économies : 66 %
Économies supplémentaires envisageables :
- Récupération de chaleur
- Remplacement du sécheur par un modèle à réfrigération
- Diminution des points d'utilisation finale.
Cas 2 : emploi d'un compresseur de puissance plus faible en dehors des heures de travail
Dans l'exemple qui précède, la compagnie avait installé un système sec de protection contre l'incendie qui consommait 5 pcm d'air comprimé en permanence, y compris pendant les fins de semaine où n'intervenait aucune production. Cette demande d'air entraînait le fonctionnement d'un compresseur de 100 HP régulé par modulation pendant 2 760 heures de plus chaque année.
Charge de l'usine pendant la fin de semaine :
- Purge du sécheur : 150 pcm
- Fuites : 100 pcm
- Purgeurs : 5 pcm
- Système de protection incendie : 5 pcm
Avant
- Puissance du compresseur de 100 HP régulé en modulation à 260 pcm = 76 kW
- Énergie totale consommée annuellement 76 kW× 2 760 h = 209 760 kWh
- Coût d'exploitation = 20 976 $ par an (à 0,10 $ le kWh)
Après
- Utilisation d'un petit compresseur à piston de 5 HP (4,25 kW) d'un débit de 15 pcm pour le seul système de protection incendie (isolé par un clapet de non-retour).
Consommation en fonctionnement :
- " Charge de 5 pcm /capacité de 15 pcm × 4,25 kW = 1,42 kW × 2 760 h = 3 910 kWh
- Coût annuel = 391 $
- Économies annuelles = 20 585 $ (98 %).
Cas 3: régulation tout ou rien comparée à régulation en charge/à vide
Un petit concessionnaire automobile envisage de moderniser son système d'air comprimé. Le système actuel est constitué d'un compresseur à piston de 15 HP d'une capacité de 50 pcm à 175 psi. Lorsqu'il fonctionne, l'appareil absorbe 13 kW en moyenne et il est installé sur un réservoir de 80 gallons.
Les données de charge moyenne de l'installation ont été enregistrées et l'on a déterminé que le débit moyen était de 10 pcm avec un débit de pointe de 50 pcm. L'air produit par le compresseur traverse deux filtres montés en série (un filtre à particules et un filtre à coalescence) puis est séché dans un sécheur de 75 pcm à détente directe avec robinet de dérivation des gaz chauds consommant 0,88 kW. La chute de pression dans le sécheur d'air est égale à 4 psi alors que la pression différentielle des filtres atteint en tout 4 psi. Le sécheur est équipé d'un purgeur programmé qui consomme en moyenne 2 pcm. Le système fonctionne à une pression moyenne de 145 psi pendant 3 745 heures par an. Le tarif d'électricité mixte est de 10 cents le kWh.
Le concessionnaire envisage d'acheter un compresseur à vis de 15 HP pour remplacer son compresseur à piston en mauvais état. Le vendeur de compresseurs signale qu'un nouveau compresseur à vis offre un meilleur rendement vu qu'il est capable de produire 58 pcm à 150 psi à 13,5 kW. Selon la planification, il est prévu d'installer le nouveau compresseur sur le même réservoir de 80 gallons, d'utiliser les mêmes filtres et le même sécheur, et de fonctionner à une pression moyenne de 145 psi.
- Consommation du compresseur déjà existant = 13 kW × 10 pcm/50 pcm de capacité × 3 745 h = 9 737 kWh par an x 0,10 $ le kWh = 974 $ par an
- Consommation du sécheur = 0,88 kW × 3 745 h = 3 296 kWh = 330 $ par an (Note : il est très courant de voir ces sécheurs laissés en marche en permanence, soit 8 760 heures par an).
- Coût annuel total du système = 1 304 $.
Le nouveau compresseur à vis va fonctionner en mode en charge/à vide avec une capacité de stockage de 1,37 gallons US par pcm et une plage de pression de 10 psi. À cause de la chute de pression dans les filtres et dans le sécheur, le compresseur va fonctionner par cycles trop courts et rester en fonctionnement pendant toutes les heures d'exploitation. En se basant sur la courbe de rendement en charge/à vide (voir la Figure 7 à la page 3), on peut constater que le compresseur va consommer en moyenne 60 % de sa puissance nominale.
Système à régulation en charge/à vide proposé avec sécheur classique
- Consommation du compresseur proposé = 13,5 kW × 0,6 × 3 745 h= 30 335 kWh par an = 3 034 $ par an.
- Consommation du sécheur = 0,88 kW × 3 745 h = 3 296 kWh x 0,10 $ le kWh = 330 $ par an
- Coût annuel total du système = 3 364 $.
Il en coûte environ 2,5 fois plus cher pour faire fonctionner le nouveau compresseur à vis.
Variante de système à haut rendement - fonctionnement en mode tout ou rien et application de mesures d'amélioration
Mesures supplémentaires devant être mises en place :
- Pression différentielle réduite à 0,5 psi dans des filtres surdimensionnés et à 3 psi dans un nouveau sécheur à fonctionnement cyclique d'une puissance de 0,51 kW.
- Pression moyenne de refoulement du compresseur réduite à 115 psi. Le compresseur choisi s'arrête immédiatement si le nombre de démarrages du moteur est inférieur à 6 par heure.
-
Pertes de purge ramenée à zéro par l'emploi de purgeurs à dépression.
- Ajout d'un réservoir de stockage afin de réduire le nombre de démarrages du moteur à moins de 6 par heure, quel que soit le débit.
- Ajout d'un robinet de régulation pour ramener la pression dans l'atelier à une valeur constante de 100 psi.
Les mesures d'efficacité énergétique permettent de diminuer le débit moyen d'air et la puissance moyenne :
- 2 pcm de réduction pour les purgeurs
- 2 pcm dus à la réduction de la pression
- Consommation en énergie du compresseur réduite de 15 % en raison de la réduction de pression de 30 psi.
- La consommation en énergie du sécheur est désormais proportionnelle au débit.
- Consommation en énergie du compresseur proposé (refoulement à une pression plus faible) = 11,5 kW × 6 pcm/58 pcm de capacité × 3 745 h = 4 455 kWh par an x 0,10 $ le kWh = 446 $ par an.
- Consommation du sécheur = 0,5 kW× 6 pcm/80 pcm de capacité × 3 745 h = 140 kWh x 0,10 $ le kWh = 14 $ par an.
- Coût annuel total du système = 460 $.
- La consommation du système éconergétique correspond à environ 35 % de celle du système d'origine, et à 14 % de celle du système avec régulation en charge/à vide.
Prochaines étapes
L'optimisation des systèmes d'air comprimé est un processus continu. Vous lancer dans un programme d'optimisation de votre système d'air comprimé peut vous sembler une tâche presque insurmontable.
Si vous ne savez pas par où commencer, attaquez-vous aux "solutions qui sont à votre portée" comme par exemple la réparation des fuites d'air, la diminution des pressions dans le système et l'optimisation des points de consigne et réglages. Lorsque vous verrez les résultats de ces mesures (et les économies d'électricité qui s'ensuivent), faites-le savoir. La direction et vos collègues de travail voudront que vous leur parliez de votre réussite.
Grâce à ces premiers résultats, vous serez dans une meilleure position pour convaincre la direction d'investir des capitaux, d'investir dans des compresseurs plus éconergétiques, de moderniser le système de distribution et d'affecter des ressources au contrôle régulier des fuites d'air. Rappelez-vous que le système d'air comprimé un ensemble d'éléments et que la modification d'une composante ou d'un réglage risque de se répercuter ailleurs. L'astuce consiste à rééquilibrer sans cesse le système de façon à l'améliorer de façon continue.
À la conception ou à l'achat de composantes du système d'air comprimé, tenez toujours compte du coût de fonctionnement sur toute la durée de vie. Collaborez avec votre service des achats afin d'acquérir les composantes les plus éconergétiques, même si leur coût initial est plus élevé. Faites participer les employés de l'usine. Informez-les du fait que l'air comprimé n'est pas gratuit. Demandez-leur de signaler les fuites d'air. Accordez des ressources suffisantes aux services d'entretien pour la réparation des fuites d'air. Faites de ce processus un travail d'équipe.
Communiquez avec votre entreprise d'électricité locale pour obtenir un avis et des conseils additionnels en matière d'efficacité énergétique, et pour avoir de l'aide sur la façon d'effectuer des mesures sur votre système.
Glossaire
- Chute de pression
- Perte de pression dans un système d'air comprimé ou une de ses composantes, attribuable au frottement ou à un étranglement.
- Clapet antiretour
- Robinet permettant l'écoulement dans une seule direction.
- Compresseur alternatif
- Compresseur dans lequel l'élément de compression est constitué par un piston qui est animé d'un mouvement alternatif à l'intérieur d'un cylindre.
- Compresseurs volumétriques
- Compresseurs dans lesquels des volumes successifs d'air ou de gaz sont emprisonnés dans un espace clos, cet espace étant réduit par une action mécanique qui engendre une élévation de pression (compression). Ces compresseurs peuvent être du type alternatif ou du type rotatif.
- Cycle
- Série d'étapes accomplies par un compresseur avec marche à vide 1) à pleine charge; 2) en mode modulation (dans le cas des compresseurs à régulation par modulation); 3) à vide; et 4) au ralenti.
- Débit
- La quantité d'air fournie dans des conditions données et généralement exprimée en pieds cubes par minute (pcm).
- Durée de cycle
- Temps pris par un compresseur pour accomplir un cycle complet.
- En charge/à vide
- mode de fonctionnement d'un compresseur dans lequel aucun air de sortie n'est délivré car l'admission d'air est fermée ou a été modifiée pour que l'air ne puisse être emprisonné.
- Entraînement à vitesses variable
- Dispositif électronique qui fait varier la vitesse d'un moteur et permet ainsi de réaliser des économies d'énergie aux débits peu élevés.
- Étages
- Série d'étapes dans la compression de l'air ou du gaz. La plupart des compresseurs industriels possèdent deux étages.
- Filtres
- Dispositifs de séparation et d'éliminations des particules, de l'humidité ou de l'huile entraînées dans l'air.
- Fuite
- Perte involontaire d'air comprimé dans les conditions ambiantes.
- Outils pneumatiques
- Outils fonctionnant à l'air comprimé.
- Pied cube normal par minute (pcnm)
- Débit d'air libre mesuré et converti pour un ensemble normalisé de conditions de référence (14,5 psia, 68 °F, et 0 pour cent d'humidité relative).
- Pied cube par minute (pcm)
- Débit d'air volumétrique. pcm air libre - pcm d'air fournis en un point considéré et dans des conditions données de température et de pression, ramenés aux conditions ambiantes de température et de pression.
- Pieds cubes effectifs par minute (acfm)
- Débit d'air à la pression et à la température réelles de fonctionnement.
- Pleine charge
- Fonctionnement d'un compresseur à sa pleine vitesse avec aspiration totalement ouverte et débit d'air de refoulement maximal.
- Point de rosée
- Température à laquelle l'humidité contenue dans l'air va commencer à se condenser lorsque l'air est refroidi sous une pression constante. L'humidité relative à ce moment est alors de 100 pour cent.
- Pression
- Force par unité de surface, mesurée en livres par pouce carré (psi) ou en kilopascals (kPa).
- Pression absolue
- Pression totale mesurée par rapport à une pression nulle (vide parfait).
- Pression atmosphérique
- La pression ambiante mesurée pour un emplacement et une altitude considérés.
- Pression de refoulement
- Pression au raccordement de sortie d'un compresseur.
- Pression manométrique
- Pression indiquée par la plupart des instruments et indicateurs, généralement exprimées en psig (lb/po²). Pour déterminer la pression réelle ou absolue, on doit tenir compte de la pression barométrique.
- Puissance au frein
- Puissance mécanique fournie à l'arbre d'entraînement d'un moteur électrique ou d'un moteur thermique, ou puissance mécanique devant être fournie à l'arbre du compresseur pour son fonctionnement.
- Refroidissement intermédiaire
- Extraction de la chaleur de l'air ou d'un gaz entre étages d'un compresseur.
- Refroidisseur de sortie
- Échangeur de chaleur employé pour le refroidissement de l'air à la sortie d'un compresseur. Les condensats produits peuvent être éliminés par un séparateur d'humidité installé en aval du refroidisseur de sortie.
- Régulation en charge/à vide
- Méthode de régulation qui permet au compresseur de tourner à pleine charge ou à vide, l'entraînement tournant à vitesses constante.
- Régulation par modulation
- Mode de fonctionnement qui s'adapte aux variations de la demande en restreignant l'entrée d'air du compresseur proportionnellement à la demande.
- Régulation tout ou rien
- Système dans lequel la fourniture d'air comprimé est adaptée à la demande par mise en marche ou arrêt du compresseur.
- Réservoirs
- Récipient ou cuve servant au stockage d'un gaz sous pression. Les gros systèmes d'air comprimé peuvent comporter des réservoirs primaires et secondaires.
- Séquence
- Ordre dans lequel les compresseurs sont mis en service.
- Séquenceur automatique
- Dispositif qui fait fonctionner les compresseurs en séquence selon un programme établi à l'avance.
- Taux de compression
- Rapport de la pression de refoulement absolue à la pression d'aspiration absolue.
- Température de refoulement
- Température à la bride de refoulement d'un compresseur.
Documentation et références web
Ouvrages de référence
- Ressources naturelles Canada. "Compressors and Turbines" ISBN 0-662-14166-0, 1987
- Scales, William. "Best Practices for Compressed Air Systems", 2003
- US Department of Energy. "Improving Compressed Air System Performance" DEO/GO-102003-1822, 2003
Références Internet (juin 2007)
- BC Hydro Compressed Air Program www.bchydro.com/powersmart/industrial.html
- Compressed Air Challenge www.compressedairchallenge.org
- Compressed Air & Gas Institute www.cagi.org
- Hydro-Québec - Entretien préventif des compresseurs www.hydroquebec.com/business/appui_pmi/procedures_outils/compression.html
- Manitoba Hydro Compressed Air Program www.hydro.mb.ca/pop/compressed_air.shtml
Ressources naturelles Canada, Office de l'efficacité énergétique http://www.oee.nrcan.gc.ca/publications/industrial/cipec/compressed-air.pdf
Unités de mesures et facteurs de conversion
Température
Degrés Fahrenheit = (1,8 × degrés Celsius) + 32
Pression
1 bar = 14,50 lb/po² (psi)
Longueur
1 cm = 0,3937 pouce
1 m = 3,28 pieds
Volume
1 litre = 0,21997 gallons (impérial)
1 litre = 0,26417 gallons (US)
Énergie
1 kWh = 3,6 MJ
1 kWh = 3 412 Btu
Puissance
1 HP = 0,746 kW
Conseils pratiques pour optimiser les systèmes d’air comprimé
Voici une liste de dix mesures que vous pouvez prendre, améliorer ou évaluer pour démarrer votre programme d'optimisation et d'efficacité énergétique de votre système d'air comprimé :
- Identifier et réparer les fuites d'air en commençant par la plus importante.
- Mesurer les paramètres de votre système d'air comprimé et établissez une base de référence afin de déterminer ses coûts d'exploitation et son efficacité.
- Faites fonctionner le système d'air comprimé à la pression pratique la plus basse possible.
- Installez, réglez et entretenez des dispositifs de régulation du système automatiques afin de coordonner le fonctionnement des compresseurs.
- Fermer l'alimentation en air comprimé des zones, équipements et applications qui ne sont pas en activité.
- Utilisez une soufflante plutôt qu'un compresseur quand il y a lieu.
- Employez des réservoirs d'air comprimé afin de réduire la fréquence des cycles des compresseurs et d'être en mesure de répondre aux demandes de pointe.
- Installez, lorsque c'est réalisable, des tuyauteries de plus grand diamètre et des configurations de distribution en boucle.
- Gardez les équipements d'air comprimé, filtres et purgeurs à un niveau d'entretien adéquat.
- Demandez-vous constamment si l'air comprimé est bien le meilleur type d'énergie pour l'application envisagée.
Rappelez-vous d'impliquer le personnel d'exploitation et d'entretien du système d'air comprimé dans toutes les décisions de production et d'utilisation finale.
Vos observations et commentaires seraient appréciés. Veuillez nous les transmettre à l'adresse :